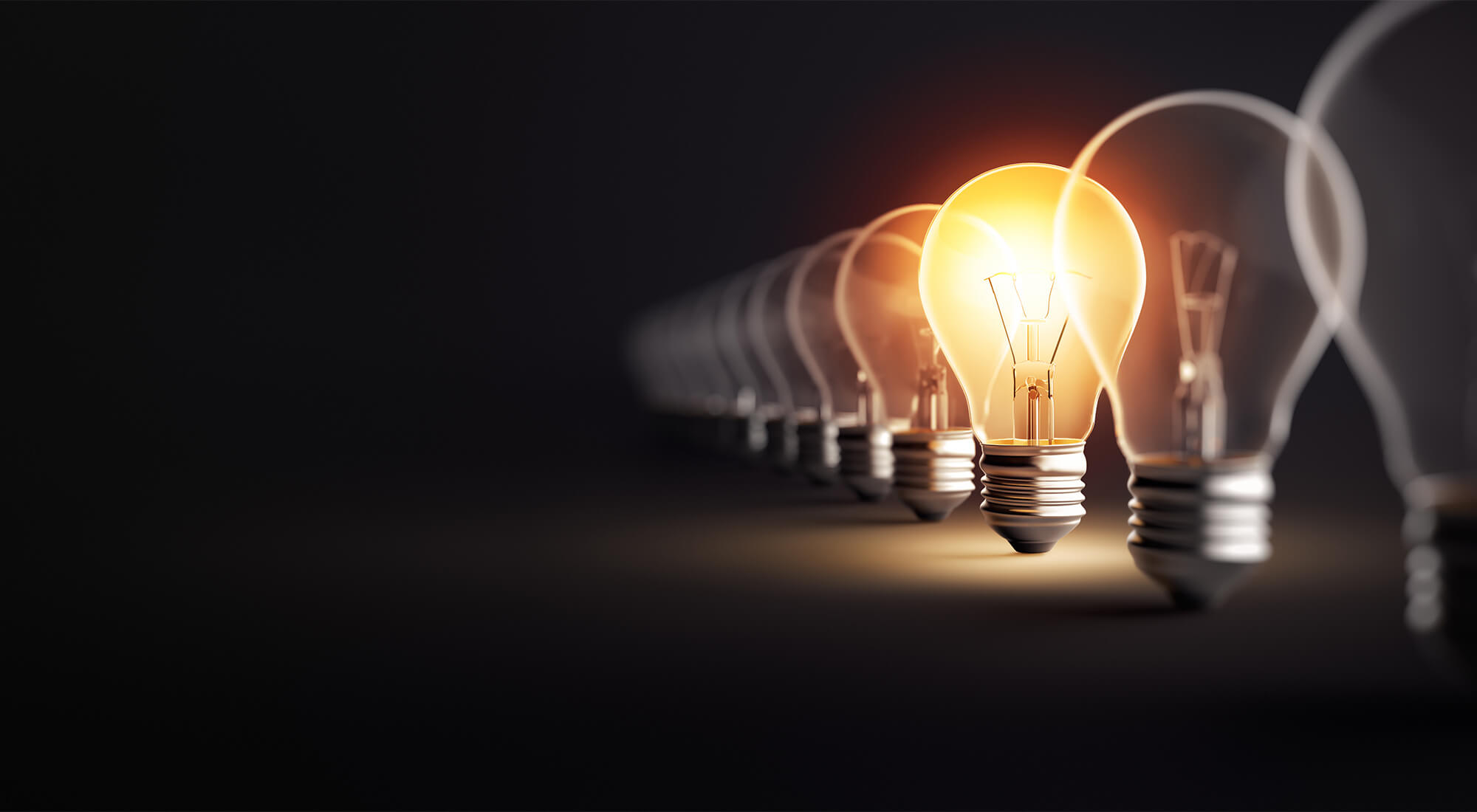
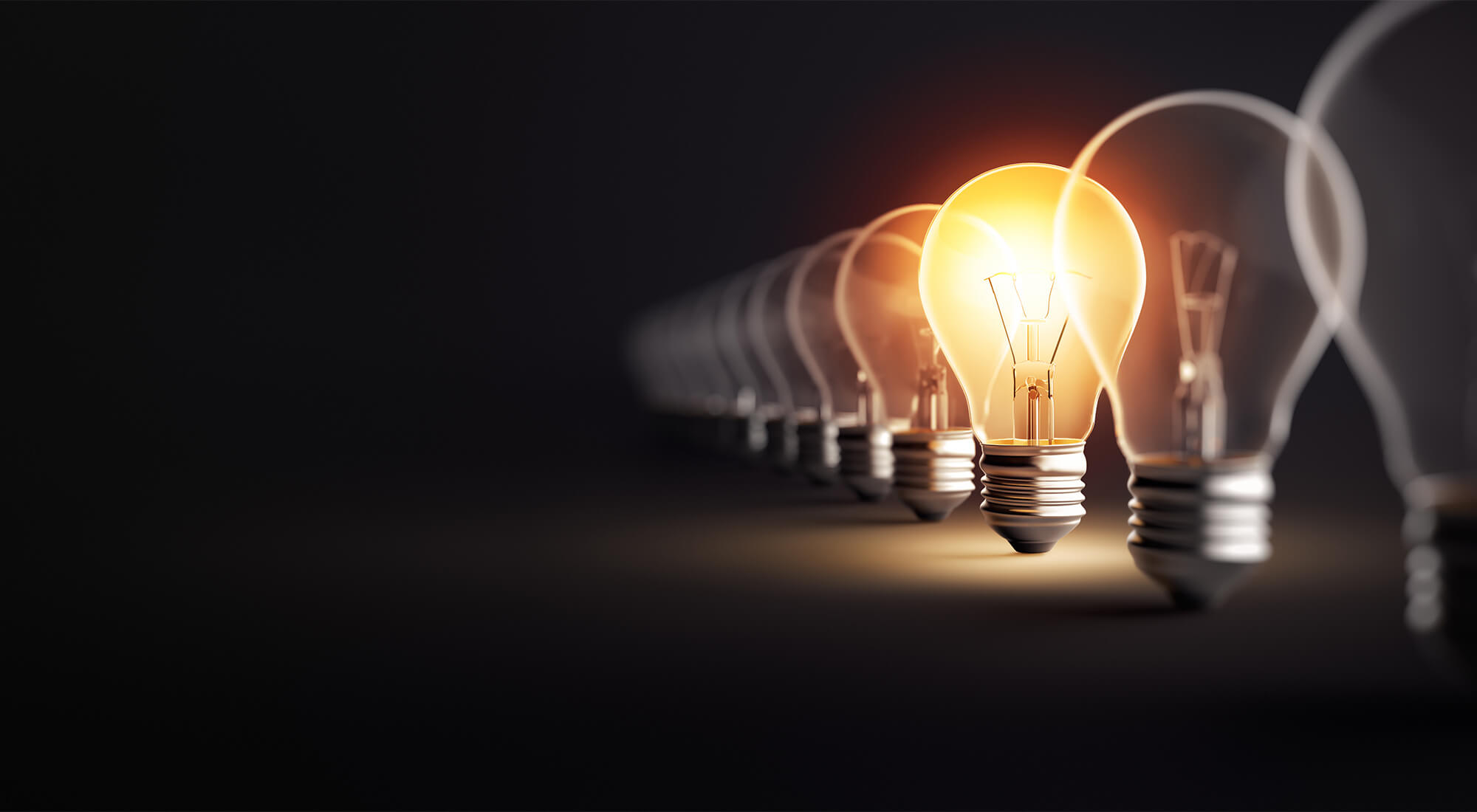
AVEVA aiming to drive sustainability by helping industries digitally transform
As an AVEVA Select partner we are proud to be the sole AVEVA distributor for the sub-Saharan region and drive the approach AVEVA is taking when it comes to sustainability.
At AVEVA, sustainability has never been higher on the agenda! Our partner is taking actions to embed sustainability into our operations and our core business strategy. They are committed to leading sustainable innovation and to work in partnership with others to make a more just, net-zero world a reality for the next generation.
They will manage sustainability through the lens of their technology handprint, operational footprint, and inclusive culture. This approach was delivered to our region in Southern Africa at our Annual X-Change User Conference that took place in May 2022.
Our media partner, Engineering News, covered this topic in further detail in an article below:
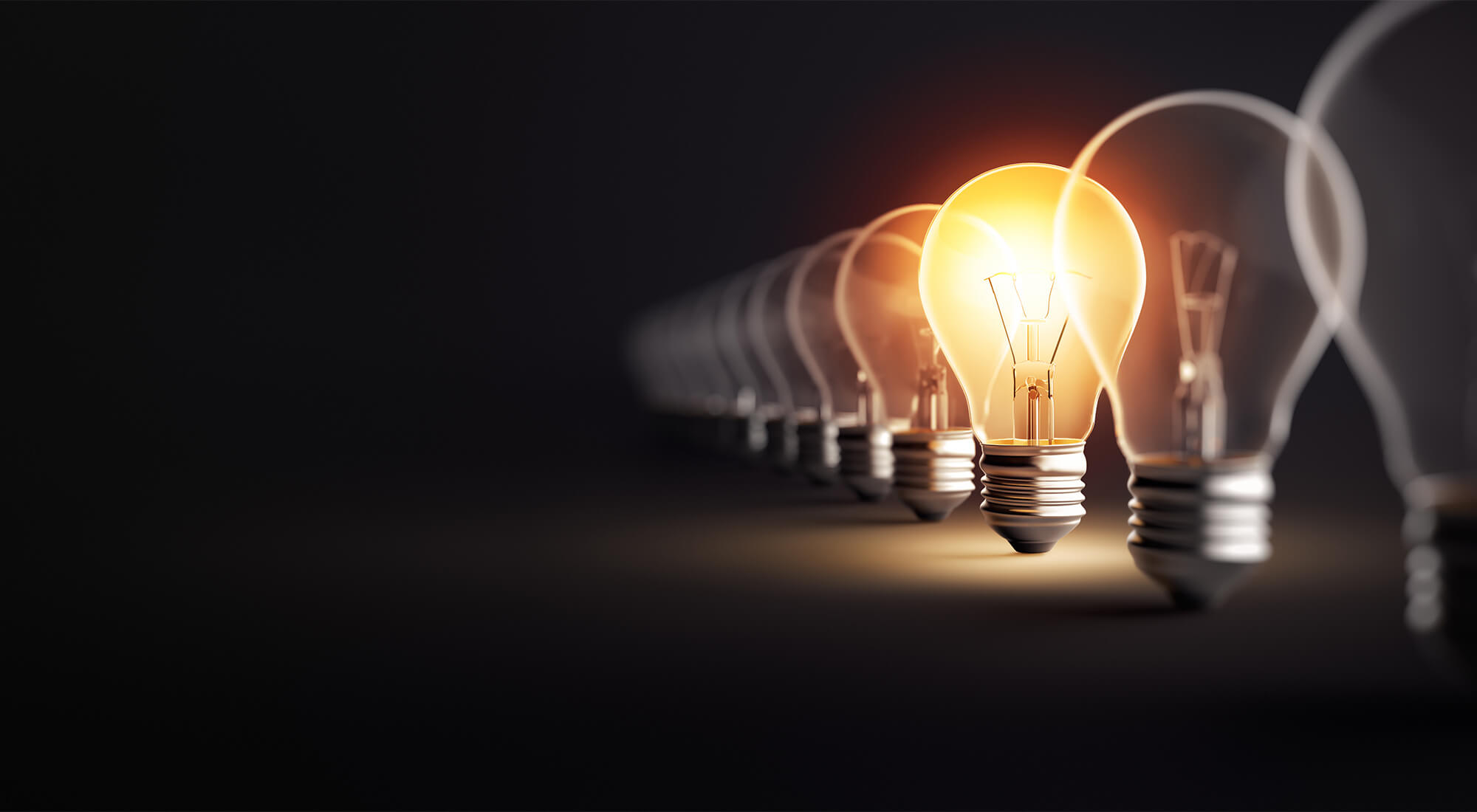
AVEVA aiming to drive sustainability by helping industries digitally transform
As an AVEVA Select partner we are proud to be the sole AVEVA distributor for the sub-Saharan region and drive the approach AVEVA is taking when it comes to sustainability.
At AVEVA, sustainability has never been higher on the agenda! Our partner is taking actions to embed sustainability into our operations and our core business strategy. They are committed to leading sustainable innovation and to work in partnership with others to make a more just, net-zero world a reality for the next generation.
They will manage sustainability through the lens of their technology handprint, operational footprint, and inclusive culture. This approach was delivered to our region in Southern Africa at our Annual X-Change User Conference that took place in May 2022.
Our media partner, Engineering News, covered this topic in further detail in an article below:
“This agreement enables clients to kindle a cultural shift towards anti-fragility and resilience. It accelerates their digital transformation journeys while ensuring alignment to global and regional marketing trends as well as technology. Being chosen for the Select Partnership program is not only a testament to the value that IS³ brings to AVEVA but also signifies the incredible progress that has been made in the reshaping of the industrial automation market”
Dion Govender – CEO, Digital Industries (Pty) Ltd
“An AVEVA Select partner can leverage the full breadth of our portfolio to empower customers as they double down on their digital strategies. Designed for our distributors, the unique AVEVA Select program helps them to optimize on opportunities and support customers to succeed in their digital transition. “We are pleased to welcome IS³ to the AVEVA Select family and look forward to developing and capitalizing on mutually beneficial growth strategies.”
Kerry Grimes – Head of Global Partners, AVEVA.
About IS³
About IS³
Driven by their ability to see the limitless potential of technology to empower people and transform businesses, IS³ provides industry software solutioning and support that enables individuals, teams, and businesses to move efficiently, seamlessly, and compliantly through their digital transformation journey. Their superior industrial software solutions include production, operations, production performance, manufacturing, intelligence, and business process management.
About AVEVA
About AVEVA
AVEVA is a global leader in industrial software, driving digital transformation and sustainability. By connecting the power of information and artificial intelligence with human insight, AVEVA enables teams to use their data to unlock new value. We call this Performance Intelligence. AVEVA’s comprehensive portfolio enables more than 20,000 industrial enterprises to engineer smarter, operate better and drive sustainable efficiency. AVEVA supports customers through a trusted ecosystem that includes 5,500 partners and 5,700 certified developers around the world. The company is headquartered in Cambridge, UK, with over 6,500 employees and 90 offices in over 40 countries.
About AVEVA Select
About AVEVA Select
The AVEVA Select program is designed for partners with full access to AVEVA’s comprehensive software portfolio, enabling them to help companies accelerate their digital transformation journey. AVEVA Select aligns to both market and technology trends, with programs designed to suit every product and solution specialization in the engineering and industrial segments. By leveraging the breadth of the AVEVA software portfolio, AVEVA Select partners can now help customers simplify design, optimize production, and maximize performance.
About IS³
About AVEVA
About AVEVA Select
About IS³
Driven by their ability to see the limitless potential of technology to empower people and transform businesses, IS³ provides industry software solutioning and support that enables individuals, teams, and businesses to move efficiently, seamlessly, and compliantly through their digital transformation journey. Their superior industrial software solutions include production, operations, production performance, manufacturing, intelligence, and business process management.
About AVEVA
AVEVA is a global leader in industrial software, driving digital transformation and sustainability. By connecting the power of information and artificial intelligence with human insight, AVEVA enables teams to use their data to unlock new value. We call this Performance Intelligence. AVEVA’s comprehensive portfolio enables more than 20,000 industrial enterprises to engineer smarter, operate better and drive sustainable efficiency. AVEVA supports customers through a trusted ecosystem that includes 5,500 partners and 5,700 certified developers around the world. The company is headquartered in Cambridge, UK, with over 6,500 employees and 90 offices in over 40 countries.
About AVEVA Select
The AVEVA Select program is designed for partners with full access to AVEVA’s comprehensive software portfolio, enabling them to help companies accelerate their digital transformation journey. AVEVA Select aligns to both market and technology trends, with programs designed to suit every product and solution specialization in the engineering and industrial segments. By leveraging the breadth of the AVEVA software portfolio, AVEVA Select partners can now help customers simplify design, optimize production, and maximize performance.
IS³’s Customer Success Stories
Speak to an Expert
Contact one of our highly qualified sales representatives to see how we can assist with maximising your potential!
Transnet’s Port of Durban outwits load shedding and plans for the future
Goals
- Mitigate the effect of power outages from the national grid
- Centralised engineering
- Implementation of standards
- Stable, scalable and flexible operational information and control software platform
- Increased security
- Operational safety
- User-defined reporting facilities
- Traceable cause-and-effect scenarios
Solutions and Products
- AVEVA System Platform
- AVEVA InTouch
- AVEVA Historian
- Software Toolbox’s TOP Server I/O suite
Challenges
- Multiple contractors
- Resistance to change
- Limited time for full functional test
Results
- Power outages reduced from hours to minutes
- Secure remote access and switching of MV switchgear
- Reduced solution deployment time and costs
- Scalable solution will cater with port expansion
- Rapid data analysis through real-time reporting
- Fault finding down to the device level
- Early involvement of relevant personnel for the resolution of issues
- Remote VPN for faster service provider support.
- Fail-safe operation through extensive redundancy measure
Project Requirements and Goals
Quite obviously, the first priority was to mitigate the effects of load shedding and minimise the downtime of port operations through the monitoring and control of the electrical grid network and generators. But it soon became clear that this was not the only goal.
Transnet needed a vision to keep capacity ahead of demand and this meant taking a holistic view of the port’s operational needs, which went beyond limiting the effect of power outages. This meant including the sand dredging and pumping scheme, the central fire system, the millennium tower and the air conditioning plant.
This would require a system that was scalable, adaptable and that would support quick and well-informed control decisions. The criteria included:
Centralised engineering
The system would need to be simple to maintain, able to cope with future growth and provide for the quick rollouts of projects without downtime. The original topology consisted of 15 stand-alone AVEVA (formerly Wonderware) InTouch HMI/SCADA stations distributed over the 30 square-kilometre area of the port, with each one connected to the local area PLC. Not only did this present major difficulties with updating and maintenance, but such a topology was insufficient to realistically handle the planned rapid expansions and developments at the port.
Stable industrial software platform
This would have to improve processing speed and provide redundancy on both data storage and end device communications. The speed of the network had decreased as more equipment, data, tags and systems were added to a SCADA system that was already struggling to cope because of the lack of a supportive infrastructure.
Robust and flexible security
The ability to switch power sources remotely at any site while allowing authorisation to be changed as and when and needed all within the strict 33/11/6.6 kV switching regulations.
Operational safety
The system must have the ability to step through automatic control sequences to safely set up the network and allow synchronisation of the diesel generators with the port’s grid feeders.
Improved power supply efficiency and cost
Power Factor Correction (PFC) is a key element to getting the most from available supplies, so a key requirement was that the system must be able to not only manage power factor control in local sub-station zones but also globally override and adjust PFCs where necessary, to manage total port power factor correction.
The introduction of user-defined reporting facilities
This would be based on trend data which would be used for analytical purposes.
Implementation of software standards
With the changes envisaged during the port’s expansion, it was important to introduce and maintain standards which would reduce engineering time and costs while minimising errors and rework and speeding up project deadlines.
Traceable cause-and-effect scenarios
Immediate access to real-time and historical data would help analyse what went wrong and what caused the failure.
“The introduction of standards has definitely reduced engineering time and costs and also ensured more accurate and correct work in the port.”
Warren Hofland, CSS Systems Engineer
Implementation
The port’s complex electrical system uses medium voltage (MV) circuit breakers from a variety of manufacturers, various power monitoring meters and protection relays, as well as synchronising relays and engine management controls. It is comprised of:
- Two separately located primary 33kV supply feeds from the municipality
- One 33kV ring main unit link as backup
- 33kV to 11kV transformers
- 33kV to 6.6kV transformers
- Four 2.5MVA diesel generators
- Ten power factor correction banks
- Feeders, bus couplers, regenerative cranes at the berths and more
TNPA chose systems integrator Convenient Software Solutions (CSS) to implement the extensive upgrade project because of the company’s experience and knowledge of the AVEVA ArchestrA technology, provided by IS³, and their local presence, which meant good support and access to professional services when needed.
CSS chose to continue with the IS³ | AVEVA solution set by adding System Platform based on ArchestrA technology and the real-time AVEVA Historian. This would not only integrate seamlessly with the existing InTouch systems but also ticked all the boxes of flexibility, scalability, centralised software engineering, redundancy and the enforcement of standards in TNPA’s list of system requirements.
Bearing in mind the key system requirements, the design phase included numerous meetings to establish and finalise the software structure, the network and communication layout, tag naming convention, the HMI and its navigation facilities, documentation requirements, security provisions, data logging and trending needs as well as alarm management.
“Using the agreed operational criteria, CSS then developed a thin-slice implementation as proof of concept,” says Transnet electrical engineer Johan Sauerman. “This helped to confirm that we were on the right track with respect to our overall design philosophy and that the inherent flexibility of the chosen solutions could meet our current control and information needs. Equally important was that the same solutions would meet our changing needs in the future with regard to the port’s planned expansions and increased complexity.”
“The system as it stands today is quite extensive,” says CSS systems engineer Warren Hofland. “It comprises 13 PLCs, 8 remote I/O drops, 3 servers, 13 SCADA control stations with local Application Object Server (AOS), 5 Historian Client stations, over 2000 physical I/Os and 65 SCADA/HMI screens.”
Software Toolbox’s TOP Server I/O suite is used to communicate with various equipment such as Schneider PLCs, deep-sea controllers, CAT engine control panels, GE protection relays, Landis and Gyr power meters, IFM vibration monitoring instrumentation and a Cogent OPC Datahub.
“We paid particular attention to redundancy as this was a critical requirement,” says Hofland. “40 km of redundant fibre optic network now links the key elements of the system such as the hot standby controllers and the redundant AOS peer network to 13 local stations which will fail over to the centralised AOS server in case of problems. ‘Store and forward’ functionality protects the data while a wireless VPN is used for the remote control and operation of MV switchgear and generators.”
The wealth of organised information available in the real-time Historian is designed to support operational decisions and in this regard, Transnet personnel were able to diagnose the past and plan for the future. “We have found immense value in using the historian client to access historical trend information for investigative and diagnostic purposes,” says Sauerman.
A project of this scale will naturally involve many players and this was clear from the start. So the goal was to keep one’s eye on the objective and to ensure that all the various contractors did the same while respecting one another’s contributions. “Change is always a challenge,” says Hofland. “The trick is to make it exciting rather than threatening by showing that end-user needs are truly being addressed through everybody’s collaborative contributions.”
Conclusion
Perhaps the most significant benefit of all for the TNPA is the peace of mind that the Port of Durban, the most important international import/export hub in the country, is now master of its own fate with respect to the reliability of its electrical supply. But, while the effect of power interruptions by the national grid has been reduced from hours to minutes, perhaps the wisest decision the TNPA took was to review their operational information and control infrastructure in its entirety and adopt a solution with the flexibility and scalability to deal with the port’s ambitious expansion plans.
Benefits
- Far more secure and controllable power supply to the port
- Secure remote access and switching of MV switchgear
- Centralised development environment greatly reduces solution deployment time and costs
- System capability to easily handle future port expansions
- Rapid data analysis through real-time reporting
- Fault finding down to the device level from any InTouch view station
- Accurate diagnostics enable operators to involve the right people the first time
- Remote VPN for faster service provider support
- Redundancy on historian SQL server using ‘Store and Forward’ function – provides guarantee of data trail
Routing optimisation at Saldanha’s bulk ore terminal with help from IS³ | AVEVA
The ongoing expansion of Transnet’s bulk iron ore terminal at Saldanha Bay has meant that the routing of vast quantities of material from the rail receiving stations to the shipping points had become a logistical nightmare that was expanding exponentially – and prone to expensive errors. It was time for a change.
Background
Iron ore is delivered to the port along a dedicated ore railway managed by Transnet Freight Rail (TFR) from the mines near Sishen in the Northern Cape. Several world records have been set at the Sishen mines, including the largest single blasting operation, where 7.2 million tons of rocks were broken during a single blast in April 1981. The ore is usually transported to Saldanha by trains 2.3 km long, comprising 214 wagons, each carrying 100 tons of ore, (i.e., a total of 21 400 tons per train). A train with 660 wagons recently set a new world record for the longest train and heaviest load from Sishen to Saldanha, with a total load of 68 640 tons of ore and a length of over 7.5 km.
From the rail delivery points, the iron ore is transported by conveyor to stockpiles where it is handled by stacker-reclaimers into fine, coarse and lumpy ore piles, from which it will then be transported onto ships for export on 2.5km-long conveyors.
The existing system consisted of pages upon pages of hard-wired routes which was totally user-unfriendly, unmanageable and a nightmare to update in view of the continuous expansion of the terminal. For example, the introduction of each new conveyor would result in the possibility of another 40 routes (yet another page of buttons).
Although selecting the appropriate route was an exercise in patience, it could prove useless because there was no guarantee that the selected sequence of conveyors was available for any number of reasons ,including maintenance, being in manual mode or part of another selected route.
Another consideration is that of the stakeholders. The iron ore is actually the property of various mining houses such as Kumba Iron Ore, Assmang, ArcelorMittal and Sedibeng, all of whom need to know about the status of shipments and their location (e.g., stockpiled, loaded onto ships, etc.).
Project Requirements and Goals
Quite obviously, the first priority was to mitigate the effects of load shedding and minimise the downtime of port operations through the monitoring and control of the electrical grid network and generators. But it soon became clear that this was not the only goal.
Transnet needed a vision to keep capacity ahead of demand and this meant taking a holistic view of the port’s operational needs, which went beyond limiting the effect of power outages. This meant including the sand dredging and pumping scheme, the central fire system, the millennium tower and the air conditioning plant.
This would require a system that was scalable, adaptable and that would support quick and well-informed control decisions. The criteria included:
Centralised engineering
The system would need to be simple to maintain, able to cope with future growth and provide for the quick rollouts of projects without downtime. The original topology consisted of 15 stand-alone AVEVA (formerly Wonderware) InTouch HMI/SCADA stations distributed over the 30 square-kilometre area of the port, with each one connected to the local area PLC. Not only did this present major difficulties with updating and maintenance, but such a topology was insufficient to realistically handle the planned rapid expansions and developments at the port.
Stable industrial software platform
This would have to improve processing speed and provide redundancy on both data storage and end device communications. The speed of the network had decreased as more equipment, data, tags and systems were added to a SCADA system that was already struggling to cope because of the lack of a supportive infrastructure.
Robust and flexible security
The ability to switch power sources remotely at any site while allowing authorisation to be changed as and when and needed all within the strict 33/11/6.6 kV switching regulations.
Operational safety
The system must have the ability to step through automatic control sequences to safely set up the network and allow synchronisation of the diesel generators with the port’s grid feeders.
Improved power supply efficiency and cost
Power Factor Correction (PFC) is a key element to getting the most from available supplies, so a key requirement was that the system must be able to not only manage power factor control in local sub-station zones but also globally override and adjust PFCs where necessary, to manage total port power factor correction.
The introduction of user-defined reporting facilities
This would be based on trend data which would be used for analytical purposes.
Implementation of software standards
With the changes envisaged during the port’s expansion, it was important to introduce and maintain standards which would reduce engineering time and costs while minimising errors and rework and speeding up project deadlines.
Traceable cause-and-effect scenarios
Immediate access to real-time and historical data would help analyse what went wrong and what caused the failure.
“The introduction of standards has definitely reduced engineering time and costs and also ensured more accurate and correct work in the port.”
Warren Hofland, CSS Systems Engineer
Implementation
The port’s complex electrical system uses medium voltage (MV) circuit breakers from a variety of manufacturers, various power monitoring meters and protection relays, as well as synchronising relays and engine management controls. It is comprised of:
- Two separately located primary 33kV supply feeds from the municipality
- One 33kV ring main unit link as backup
- 33kV to 11kV transformers
- 33kV to 6.6kV transformers
- Four 2.5MVA diesel generators
- Ten power factor correction banks
- Feeders, bus couplers, regenerative cranes at the berths and more
TNPA chose systems integrator Convenient Software Solutions (CSS) to implement the extensive upgrade project because of the company’s experience and knowledge of the AVEVA ArchestrA technology, provided by IS³, and their local presence, which meant good support and access to professional services when needed.
CSS chose to continue with the IS³ | AVEVA solution set by adding System Platform based on ArchestrA technology and the real-time AVEVA Historian. This would not only integrate seamlessly with the existing InTouch systems but also ticked all the boxes of flexibility, scalability, centralised software engineering, redundancy and the enforcement of standards in TNPA’s list of system requirements.
Bearing in mind the key system requirements, the design phase included numerous meetings to establish and finalise the software structure, the network and communication layout, tag naming convention, the HMI and its navigation facilities, documentation requirements, security provisions, data logging and trending needs as well as alarm management.
“Using the agreed operational criteria, CSS then developed a thin-slice implementation as proof of concept,” says Transnet electrical engineer Johan Sauerman. “This helped to confirm that we were on the right track with respect to our overall design philosophy and that the inherent flexibility of the chosen solutions could meet our current control and information needs. Equally important was that the same solutions would meet our changing needs in the future with regard to the port’s planned expansions and increased complexity.”
“The system as it stands today is quite extensive,” says CSS systems engineer Warren Hofland. “It comprises 13 PLCs, 8 remote I/O drops, 3 servers, 13 SCADA control stations with local Application Object Server (AOS), 5 Historian Client stations, over 2000 physical I/Os and 65 SCADA/HMI screens.”
Software Toolbox’s TOP Server I/O suite is used to communicate with various equipment such as Schneider PLCs, deep-sea controllers, CAT engine control panels, GE protection relays, Landis and Gyr power meters, IFM vibration monitoring instrumentation and a Cogent OPC Datahub.
“We paid particular attention to redundancy as this was a critical requirement,” says Hofland. “40 km of redundant fibre optic network now links the key elements of the system such as the hot standby controllers and the redundant AOS peer network to 13 local stations which will fail over to the centralised AOS server in case of problems. ‘Store and forward’ functionality protects the data while a wireless VPN is used for the remote control and operation of MV switchgear and generators.”
The wealth of organised information available in the real-time Historian is designed to support operational decisions and in this regard, Transnet personnel were able to diagnose the past and plan for the future. “We have found immense value in using the historian client to access historical trend information for investigative and diagnostic purposes,” says Sauerman.
A project of this scale will naturally involve many players and this was clear from the start. So the goal was to keep one’s eye on the objective and to ensure that all the various contractors did the same while respecting one another’s contributions. “Change is always a challenge,” says Hofland. “The trick is to make it exciting rather than threatening by showing that end-user needs are truly being addressed through everybody’s collaborative contributions.”
Conclusion
Perhaps the most significant benefit of all for the TNPA is the peace of mind that the Port of Durban, the most important international import/export hub in the country, is now master of its own fate with respect to the reliability of its electrical supply. But, while the effect of power interruptions by the national grid has been reduced from hours to minutes, perhaps the wisest decision the TNPA took was to review their operational information and control infrastructure in its entirety and adopt a solution with the flexibility and scalability to deal with the port’s ambitious expansion plans.
Benefits
- Far more secure and controllable power supply to the port
- Secure remote access and switching of MV switchgear
- Centralised development environment greatly reduces solution deployment time and costs
- System capability to easily handle future port expansions
- Rapid data analysis through real-time reporting
- Fault finding down to the device level from any InTouch view station
- Accurate diagnostics enable operators to involve the right people the first time
- Remote VPN for faster service provider support
- Redundancy on historian SQL server using ‘Store and Forward’ function – provides guarantee of data trail
Routing optimisation at Saldanha’s bulk ore terminal with help from IS³ | AVEVA
The ongoing expansion of Transnet’s bulk iron ore terminal at Saldanha Bay has meant that the routing of vast quantities of material from the rail receiving stations to the shipping points had become a logistical nightmare that was expanding exponentially – and prone to expensive errors. It was time for a change.
Background
Iron ore is delivered to the port along a dedicated ore railway managed by Transnet Freight Rail (TFR) from the mines near Sishen in the Northern Cape. Several world records have been set at the Sishen mines, including the largest single blasting operation, where 7.2 million tons of rocks were broken during a single blast in April 1981. The ore is usually transported to Saldanha by trains 2.3 km long, comprising 214 wagons, each carrying 100 tons of ore, (i.e., a total of 21 400 tons per train). A train with 660 wagons recently set a new world record for the longest train and heaviest load from Sishen to Saldanha, with a total load of 68 640 tons of ore and a length of over 7.5 km.
From the rail delivery points, the iron ore is transported by conveyor to stockpiles where it is handled by stacker-reclaimers into fine, coarse and lumpy ore piles, from which it will then be transported onto ships for export on 2.5km-long conveyors.
The existing system consisted of pages upon pages of hard-wired routes which was totally user-unfriendly, unmanageable and a nightmare to update in view of the continuous expansion of the terminal. For example, the introduction of each new conveyor would result in the possibility of another 40 routes (yet another page of buttons).
Although selecting the appropriate route was an exercise in patience, it could prove useless because there was no guarantee that the selected sequence of conveyors was available for any number of reasons ,including maintenance, being in manual mode or part of another selected route.
Another consideration is that of the stakeholders. The iron ore is actually the property of various mining houses such as Kumba Iron Ore, Assmang, ArcelorMittal and Sedibeng, all of whom need to know about the status of shipments and their location (e.g., stockpiled, loaded onto ships, etc.).
Project Requirements and Goals
Quite obviously, the first priority was to mitigate the effects of load shedding and minimise the downtime of port operations through the monitoring and control of the electrical grid network and generators. But it soon became clear that this was not the only goal.
Transnet needed a vision to keep capacity ahead of demand and this meant taking a holistic view of the port’s operational needs, which went beyond limiting the effect of power outages. This meant including the sand dredging and pumping scheme, the central fire system, the millennium tower and the air conditioning plant.
This would require a system that was scalable, adaptable and that would support quick and well-informed control decisions. The criteria included:
Centralised engineering
The system would need to be simple to maintain, able to cope with future growth and provide for the quick rollouts of projects without downtime. The original topology consisted of 15 stand-alone AVEVA (formerly Wonderware) InTouch HMI/SCADA stations distributed over the 30 square-kilometre area of the port, with each one connected to the local area PLC. Not only did this present major difficulties with updating and maintenance, but such a topology was insufficient to realistically handle the planned rapid expansions and developments at the port.
Stable industrial software platform
This would have to improve processing speed and provide redundancy on both data storage and end device communications. The speed of the network had decreased as more equipment, data, tags and systems were added to a SCADA system that was already struggling to cope because of the lack of a supportive infrastructure.
Robust and flexible security
The ability to switch power sources remotely at any site while allowing authorisation to be changed as and when and needed all within the strict 33/11/6.6 kV switching regulations.
Operational safety
The system must have the ability to step through automatic control sequences to safely set up the network and allow synchronisation of the diesel generators with the port’s grid feeders.
Improved power supply efficiency and cost
Power Factor Correction (PFC) is a key element to getting the most from available supplies, so a key requirement was that the system must be able to not only manage power factor control in local sub-station zones but also globally override and adjust PFCs where necessary, to manage total port power factor correction.
The introduction of user-defined reporting facilities
This would be based on trend data which would be used for analytical purposes.
Implementation of software standards
With the changes envisaged during the port’s expansion, it was important to introduce and maintain standards which would reduce engineering time and costs while minimising errors and rework and speeding up project deadlines.
Traceable cause-and-effect scenarios
Immediate access to real-time and historical data would help analyse what went wrong and what caused the failure.
“The introduction of standards has definitely reduced engineering time and costs and also ensured more accurate and correct work in the port.”
Warren Hofland, CSS Systems Engineer
Implementation
The port’s complex electrical system uses medium voltage (MV) circuit breakers from a variety of manufacturers, various power monitoring meters and protection relays, as well as synchronising relays and engine management controls. It is comprised of:
- Two separately located primary 33kV supply feeds from the municipality
- One 33kV ring main unit link as backup
- 33kV to 11kV transformers
- 33kV to 6.6kV transformers
- Four 2.5MVA diesel generators
- Ten power factor correction banks
- Feeders, bus couplers, regenerative cranes at the berths and more
TNPA chose systems integrator Convenient Software Solutions (CSS) to implement the extensive upgrade project because of the company’s experience and knowledge of the AVEVA ArchestrA technology, provided by IS³, and their local presence, which meant good support and access to professional services when needed.
CSS chose to continue with the IS³ | AVEVA solution set by adding System Platform based on ArchestrA technology and the real-time AVEVA Historian. This would not only integrate seamlessly with the existing InTouch systems but also ticked all the boxes of flexibility, scalability, centralised software engineering, redundancy and the enforcement of standards in TNPA’s list of system requirements.
Bearing in mind the key system requirements, the design phase included numerous meetings to establish and finalise the software structure, the network and communication layout, tag naming convention, the HMI and its navigation facilities, documentation requirements, security provisions, data logging and trending needs as well as alarm management.
“Using the agreed operational criteria, CSS then developed a thin-slice implementation as proof of concept,” says Transnet electrical engineer Johan Sauerman. “This helped to confirm that we were on the right track with respect to our overall design philosophy and that the inherent flexibility of the chosen solutions could meet our current control and information needs. Equally important was that the same solutions would meet our changing needs in the future with regard to the port’s planned expansions and increased complexity.”
“The system as it stands today is quite extensive,” says CSS systems engineer Warren Hofland. “It comprises 13 PLCs, 8 remote I/O drops, 3 servers, 13 SCADA control stations with local Application Object Server (AOS), 5 Historian Client stations, over 2000 physical I/Os and 65 SCADA/HMI screens.”
Software Toolbox’s TOP Server I/O suite is used to communicate with various equipment such as Schneider PLCs, deep-sea controllers, CAT engine control panels, GE protection relays, Landis and Gyr power meters, IFM vibration monitoring instrumentation and a Cogent OPC Datahub.
“We paid particular attention to redundancy as this was a critical requirement,” says Hofland. “40 km of redundant fibre optic network now links the key elements of the system such as the hot standby controllers and the redundant AOS peer network to 13 local stations which will fail over to the centralised AOS server in case of problems. ‘Store and forward’ functionality protects the data while a wireless VPN is used for the remote control and operation of MV switchgear and generators.”
The wealth of organised information available in the real-time Historian is designed to support operational decisions and in this regard, Transnet personnel were able to diagnose the past and plan for the future. “We have found immense value in using the historian client to access historical trend information for investigative and diagnostic purposes,” says Sauerman.
A project of this scale will naturally involve many players and this was clear from the start. So the goal was to keep one’s eye on the objective and to ensure that all the various contractors did the same while respecting one another’s contributions. “Change is always a challenge,” says Hofland. “The trick is to make it exciting rather than threatening by showing that end-user needs are truly being addressed through everybody’s collaborative contributions.”
Conclusion
Perhaps the most significant benefit of all for the TNPA is the peace of mind that the Port of Durban, the most important international import/export hub in the country, is now master of its own fate with respect to the reliability of its electrical supply. But, while the effect of power interruptions by the national grid has been reduced from hours to minutes, perhaps the wisest decision the TNPA took was to review their operational information and control infrastructure in its entirety and adopt a solution with the flexibility and scalability to deal with the port’s ambitious expansion plans.
Benefits
- Far more secure and controllable power supply to the port
- Secure remote access and switching of MV switchgear
- Centralised development environment greatly reduces solution deployment time and costs
- System capability to easily handle future port expansions
- Rapid data analysis through real-time reporting
- Fault finding down to the device level from any InTouch view station
- Accurate diagnostics enable operators to involve the right people the first time
- Remote VPN for faster service provider support
- Redundancy on historian SQL server using ‘Store and Forward’ function – provides guarantee of data trail