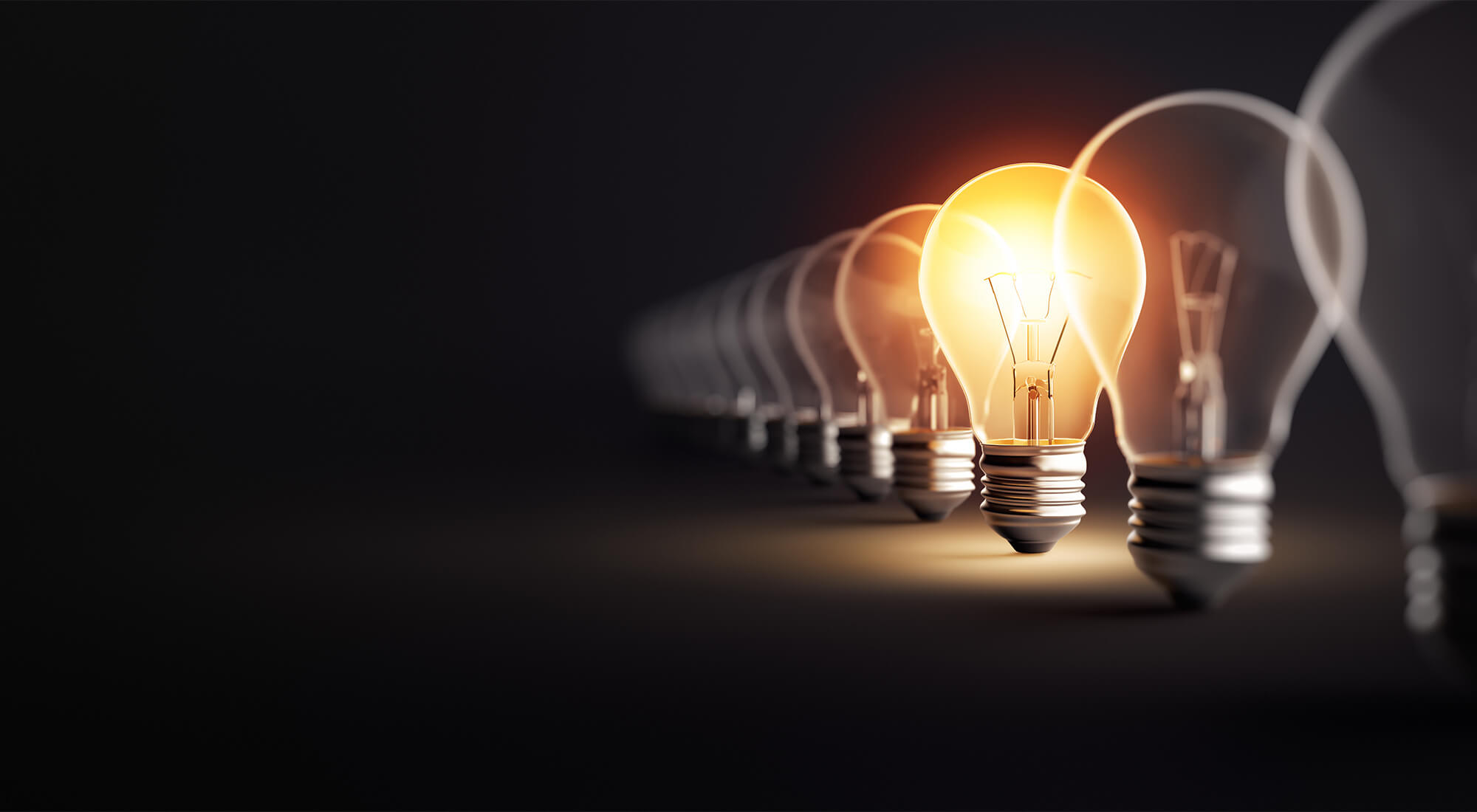
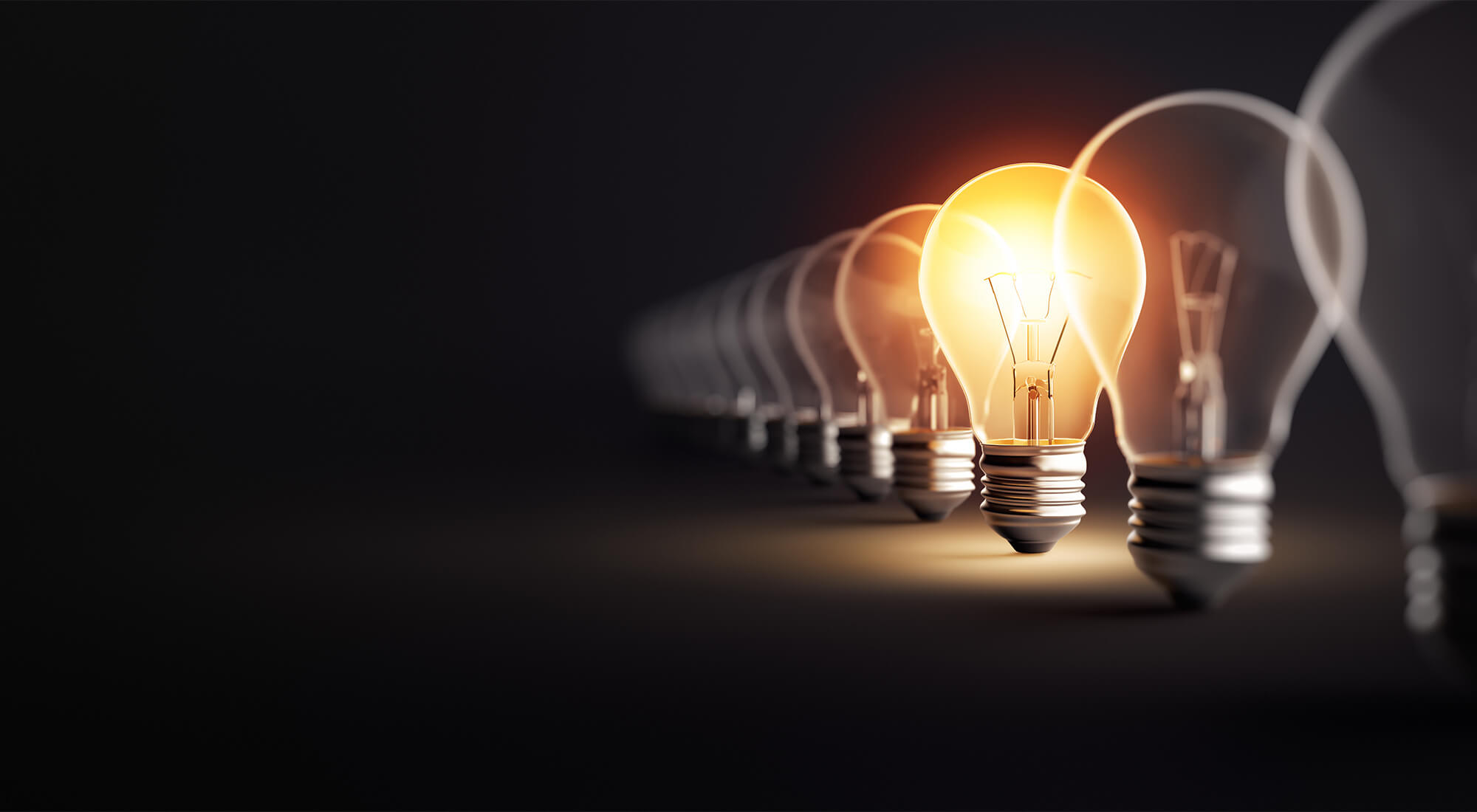
AVEVA aiming to drive sustainability by helping industries digitally transform
As an AVEVA Select partner we are proud to be the sole AVEVA distributor for the sub-Saharan region and drive the approach AVEVA is taking when it comes to sustainability.
At AVEVA, sustainability has never been higher on the agenda! Our partner is taking actions to embed sustainability into our operations and our core business strategy. They are committed to leading sustainable innovation and to work in partnership with others to make a more just, net-zero world a reality for the next generation.
They will manage sustainability through the lens of their technology handprint, operational footprint, and inclusive culture. This approach was delivered to our region in Southern Africa at our Annual X-Change User Conference that took place in May 2022.
Our media partner, Engineering News, covered this topic in further detail in an article below:
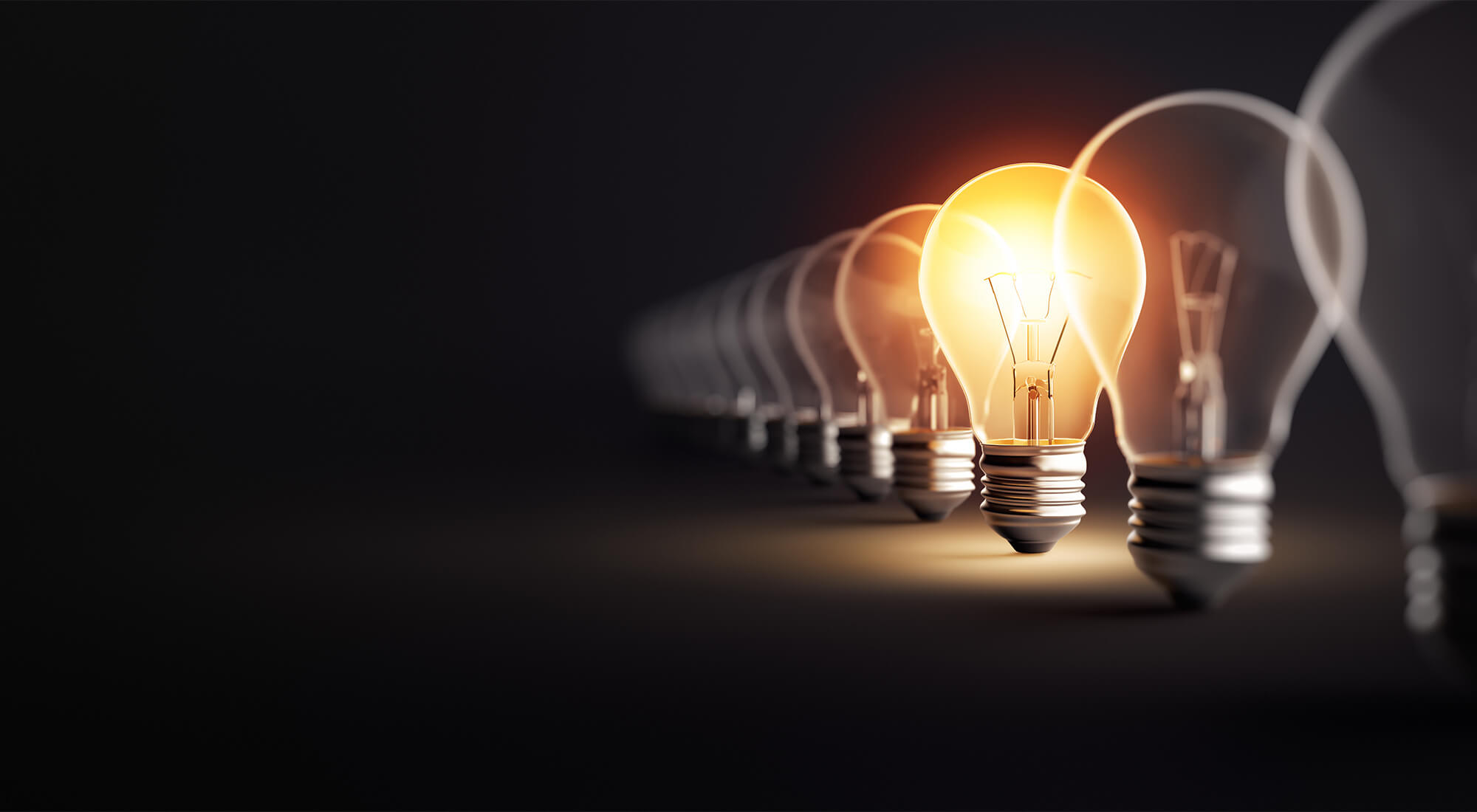
AVEVA aiming to drive sustainability by helping industries digitally transform
As an AVEVA Select partner we are proud to be the sole AVEVA distributor for the sub-Saharan region and drive the approach AVEVA is taking when it comes to sustainability.
At AVEVA, sustainability has never been higher on the agenda! Our partner is taking actions to embed sustainability into our operations and our core business strategy. They are committed to leading sustainable innovation and to work in partnership with others to make a more just, net-zero world a reality for the next generation.
They will manage sustainability through the lens of their technology handprint, operational footprint, and inclusive culture. This approach was delivered to our region in Southern Africa at our Annual X-Change User Conference that took place in May 2022.
Our media partner, Engineering News, covered this topic in further detail in an article below:
“This agreement enables clients to kindle a cultural shift towards anti-fragility and resilience. It accelerates their digital transformation journeys while ensuring alignment to global and regional marketing trends as well as technology. Being chosen for the Select Partnership program is not only a testament to the value that IS³ brings to AVEVA but also signifies the incredible progress that has been made in the reshaping of the industrial automation market”
Dion Govender – CEO, Digital Industries (Pty) Ltd
“An AVEVA Select partner can leverage the full breadth of our portfolio to empower customers as they double down on their digital strategies. Designed for our distributors, the unique AVEVA Select program helps them to optimize on opportunities and support customers to succeed in their digital transition. “We are pleased to welcome IS³ to the AVEVA Select family and look forward to developing and capitalizing on mutually beneficial growth strategies.”
Kerry Grimes – Head of Global Partners, AVEVA.
About IS³
About IS³
Driven by their ability to see the limitless potential of technology to empower people and transform businesses, IS³ provides industry software solutioning and support that enables individuals, teams, and businesses to move efficiently, seamlessly, and compliantly through their digital transformation journey. Their superior industrial software solutions include production, operations, production performance, manufacturing, intelligence, and business process management.
About AVEVA
About AVEVA
AVEVA is a global leader in industrial software, driving digital transformation and sustainability. By connecting the power of information and artificial intelligence with human insight, AVEVA enables teams to use their data to unlock new value. We call this Performance Intelligence. AVEVA’s comprehensive portfolio enables more than 20,000 industrial enterprises to engineer smarter, operate better and drive sustainable efficiency. AVEVA supports customers through a trusted ecosystem that includes 5,500 partners and 5,700 certified developers around the world. The company is headquartered in Cambridge, UK, with over 6,500 employees and 90 offices in over 40 countries.
About AVEVA Select
About AVEVA Select
The AVEVA Select program is designed for partners with full access to AVEVA’s comprehensive software portfolio, enabling them to help companies accelerate their digital transformation journey. AVEVA Select aligns to both market and technology trends, with programs designed to suit every product and solution specialization in the engineering and industrial segments. By leveraging the breadth of the AVEVA software portfolio, AVEVA Select partners can now help customers simplify design, optimize production, and maximize performance.
About IS³
About AVEVA
About AVEVA Select
About IS³
Driven by their ability to see the limitless potential of technology to empower people and transform businesses, IS³ provides industry software solutioning and support that enables individuals, teams, and businesses to move efficiently, seamlessly, and compliantly through their digital transformation journey. Their superior industrial software solutions include production, operations, production performance, manufacturing, intelligence, and business process management.
About AVEVA
AVEVA is a global leader in industrial software, driving digital transformation and sustainability. By connecting the power of information and artificial intelligence with human insight, AVEVA enables teams to use their data to unlock new value. We call this Performance Intelligence. AVEVA’s comprehensive portfolio enables more than 20,000 industrial enterprises to engineer smarter, operate better and drive sustainable efficiency. AVEVA supports customers through a trusted ecosystem that includes 5,500 partners and 5,700 certified developers around the world. The company is headquartered in Cambridge, UK, with over 6,500 employees and 90 offices in over 40 countries.
About AVEVA Select
The AVEVA Select program is designed for partners with full access to AVEVA’s comprehensive software portfolio, enabling them to help companies accelerate their digital transformation journey. AVEVA Select aligns to both market and technology trends, with programs designed to suit every product and solution specialization in the engineering and industrial segments. By leveraging the breadth of the AVEVA software portfolio, AVEVA Select partners can now help customers simplify design, optimize production, and maximize performance.
IS³’s Customer Success Stories
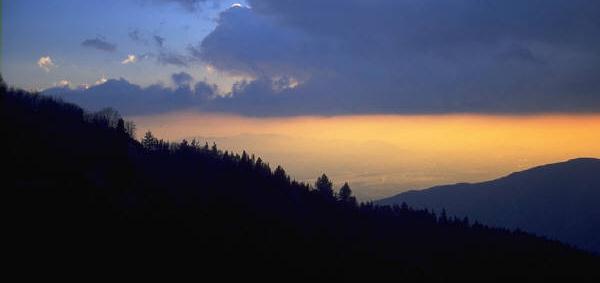
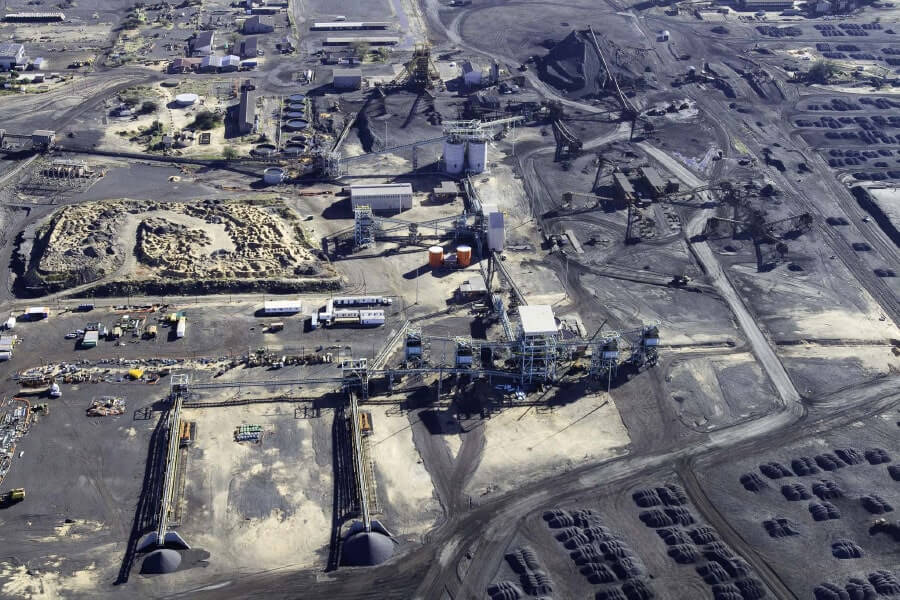
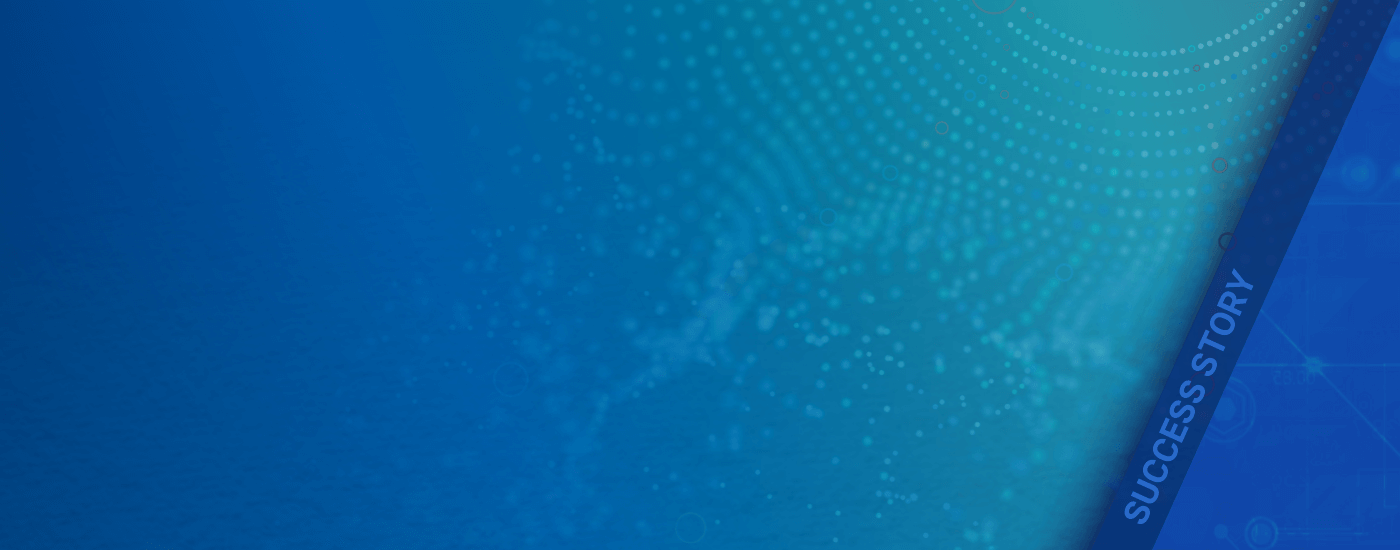
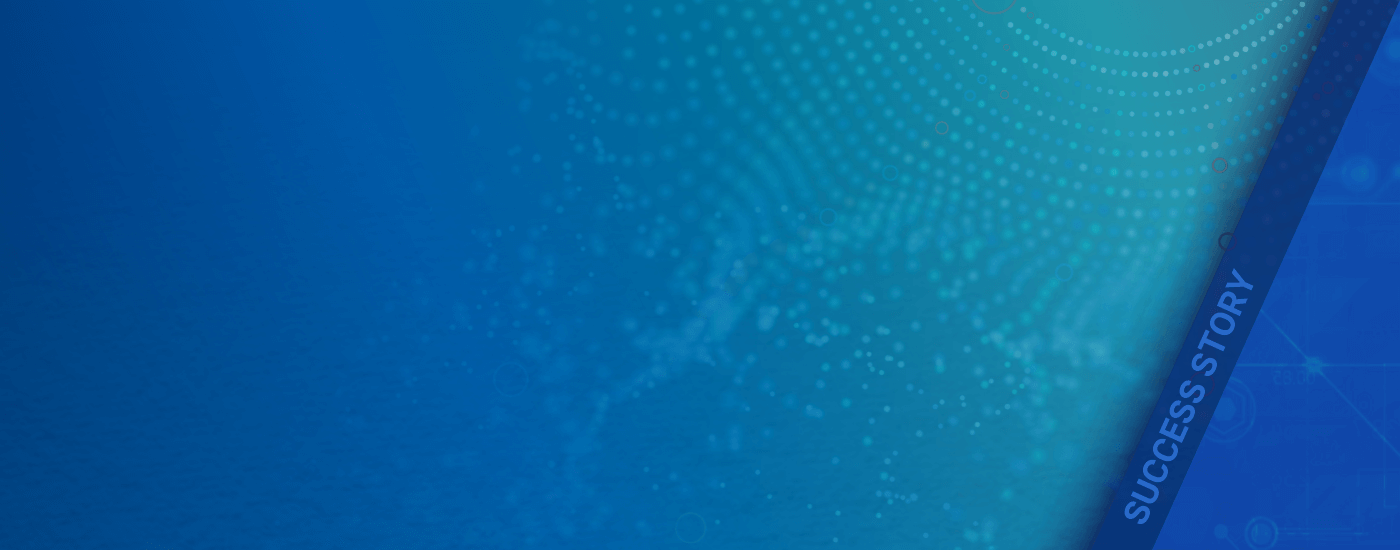
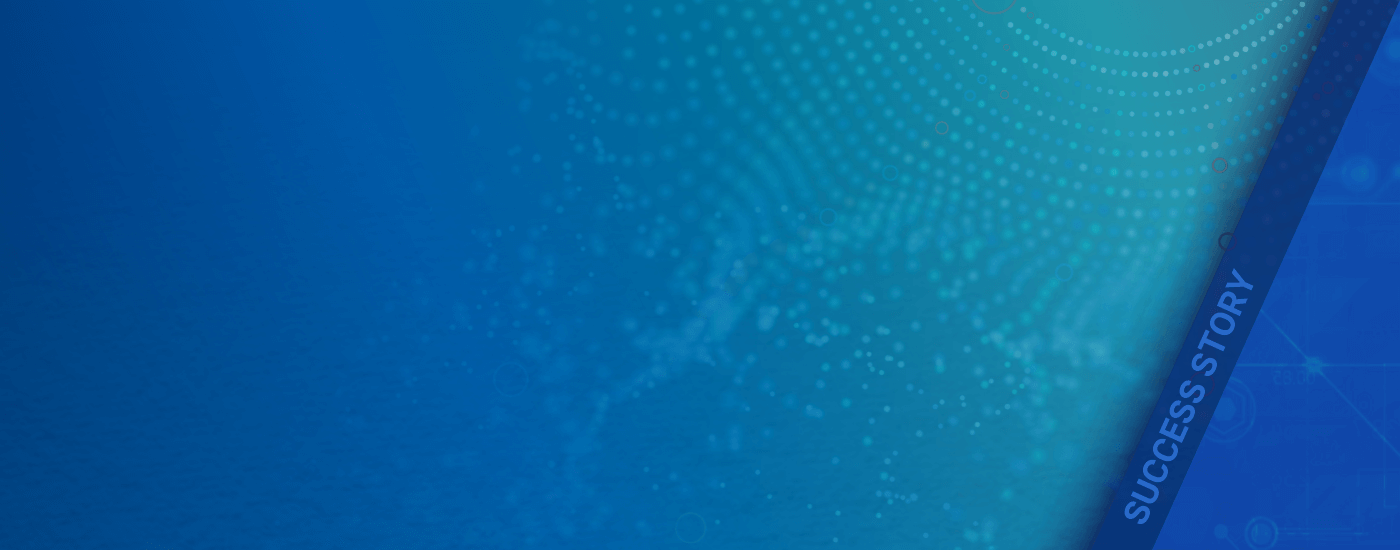
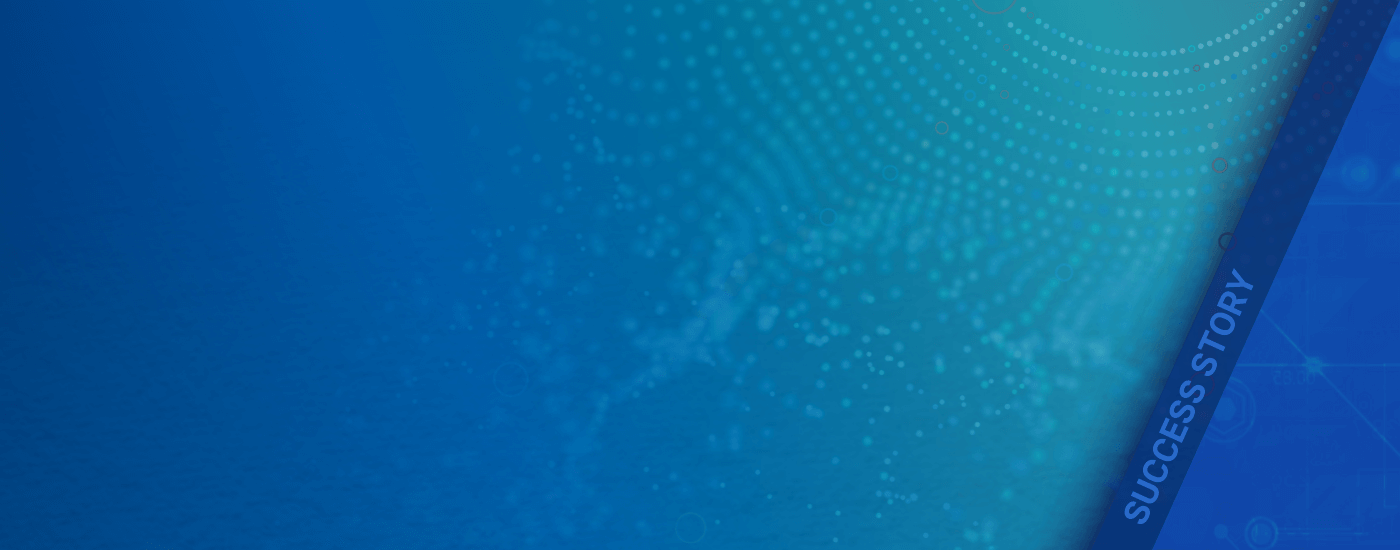
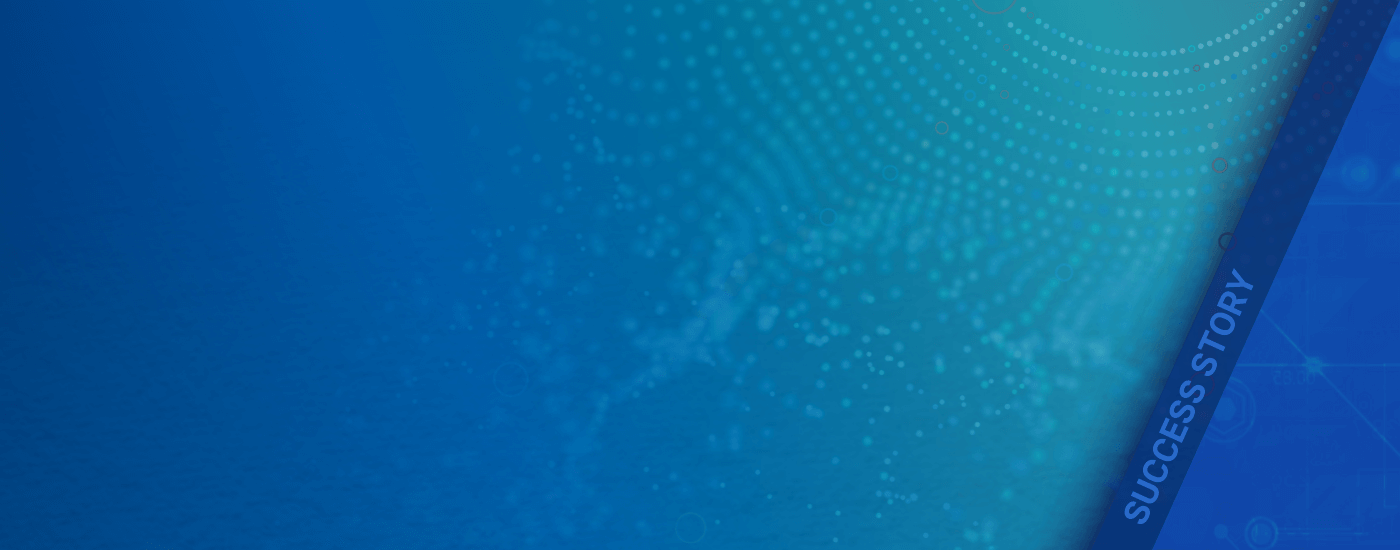
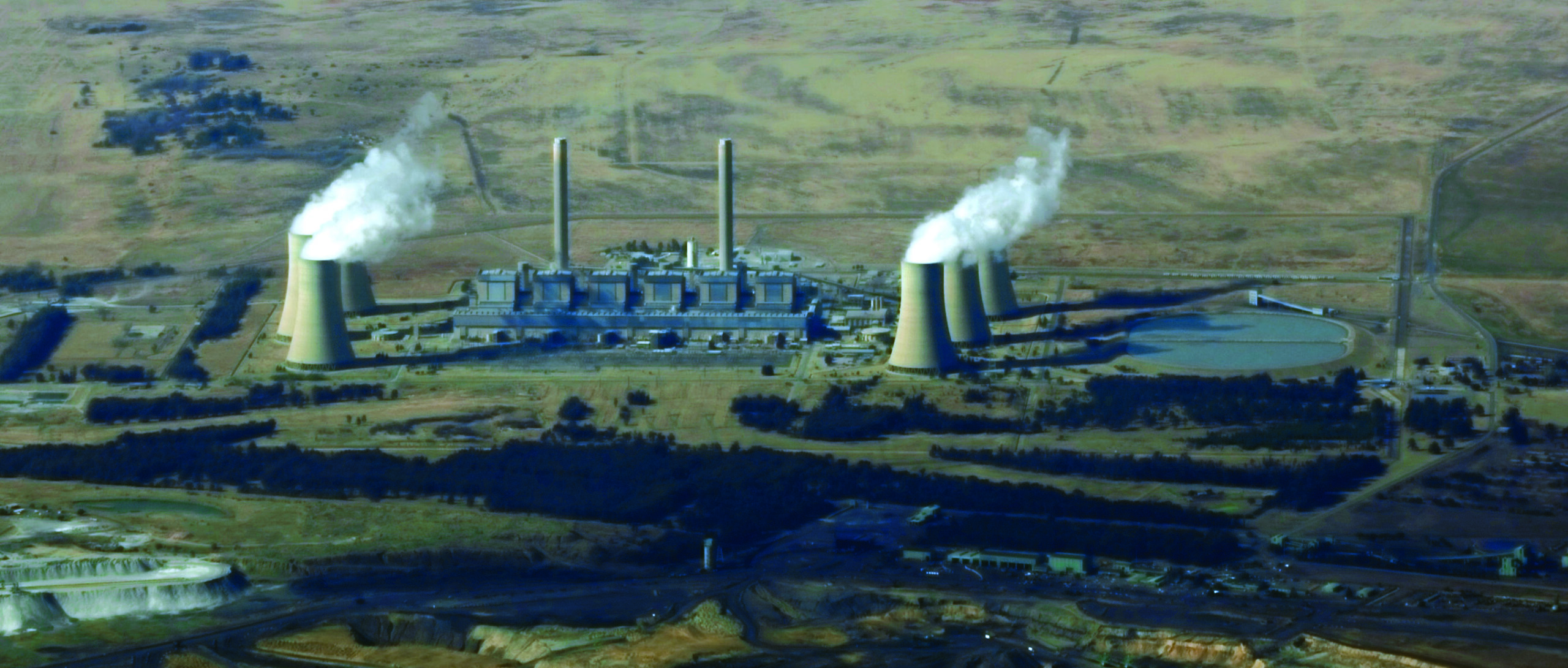
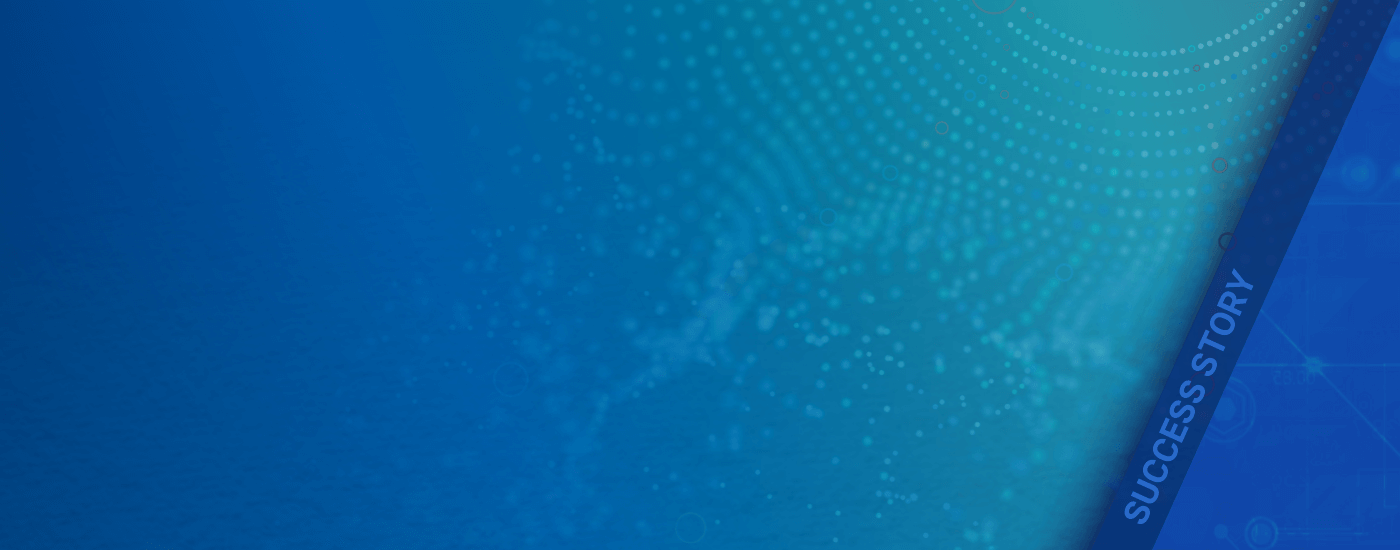
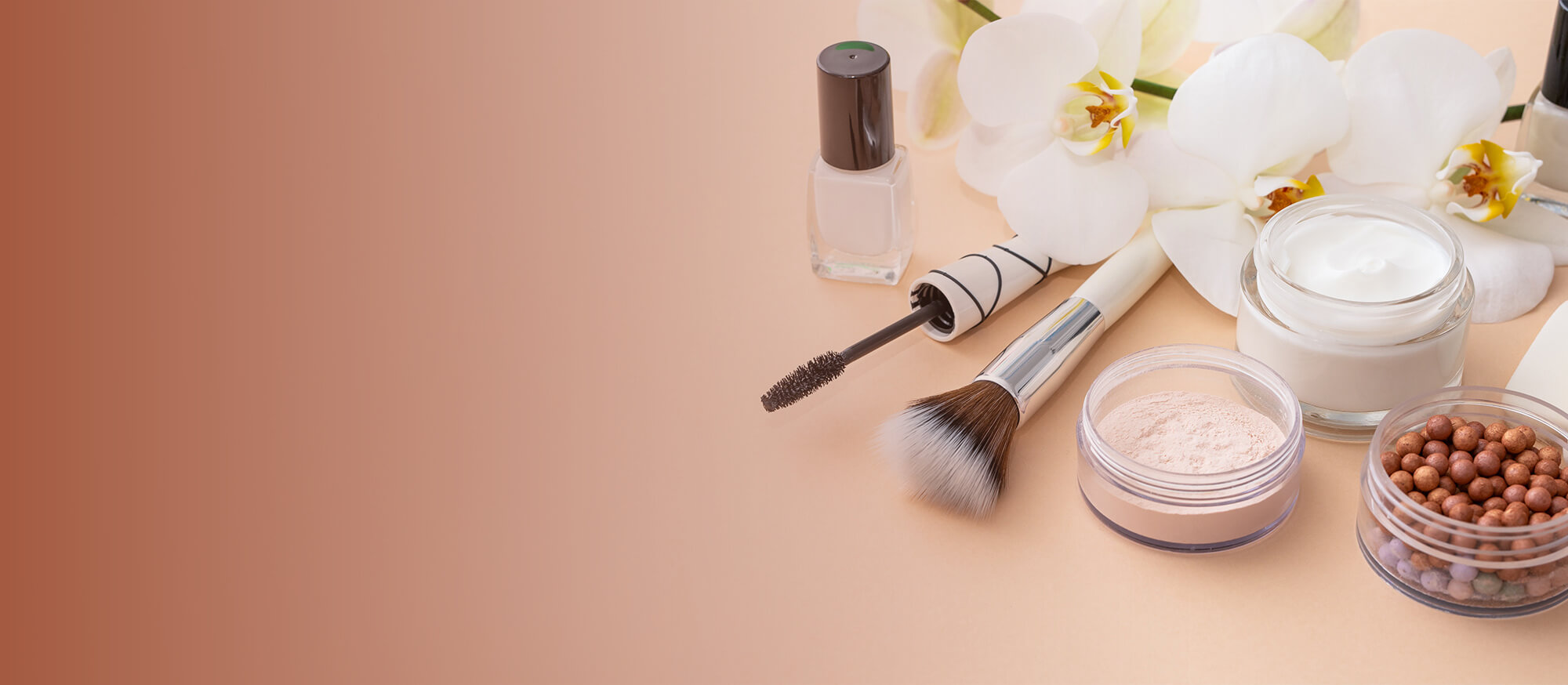
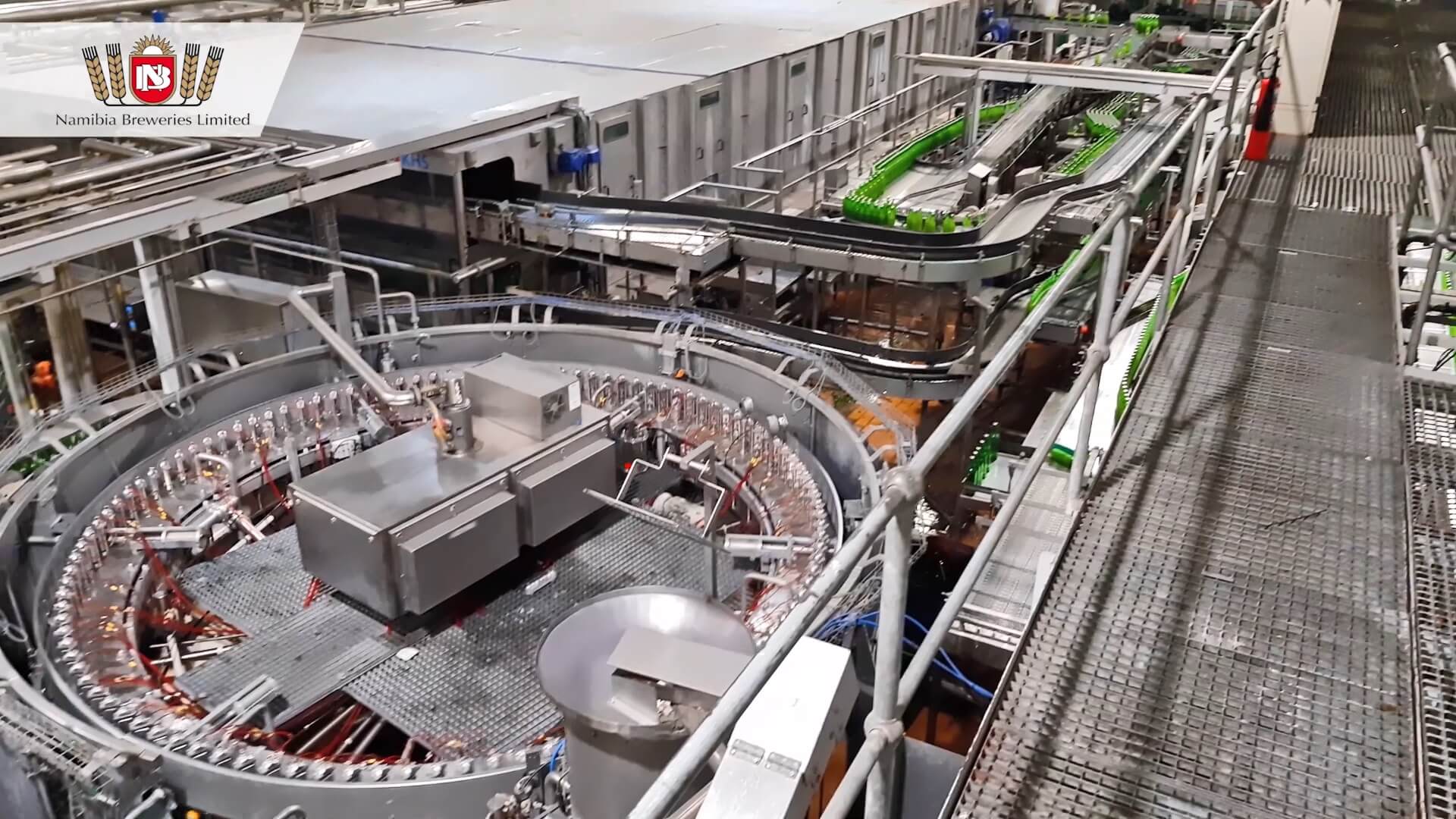
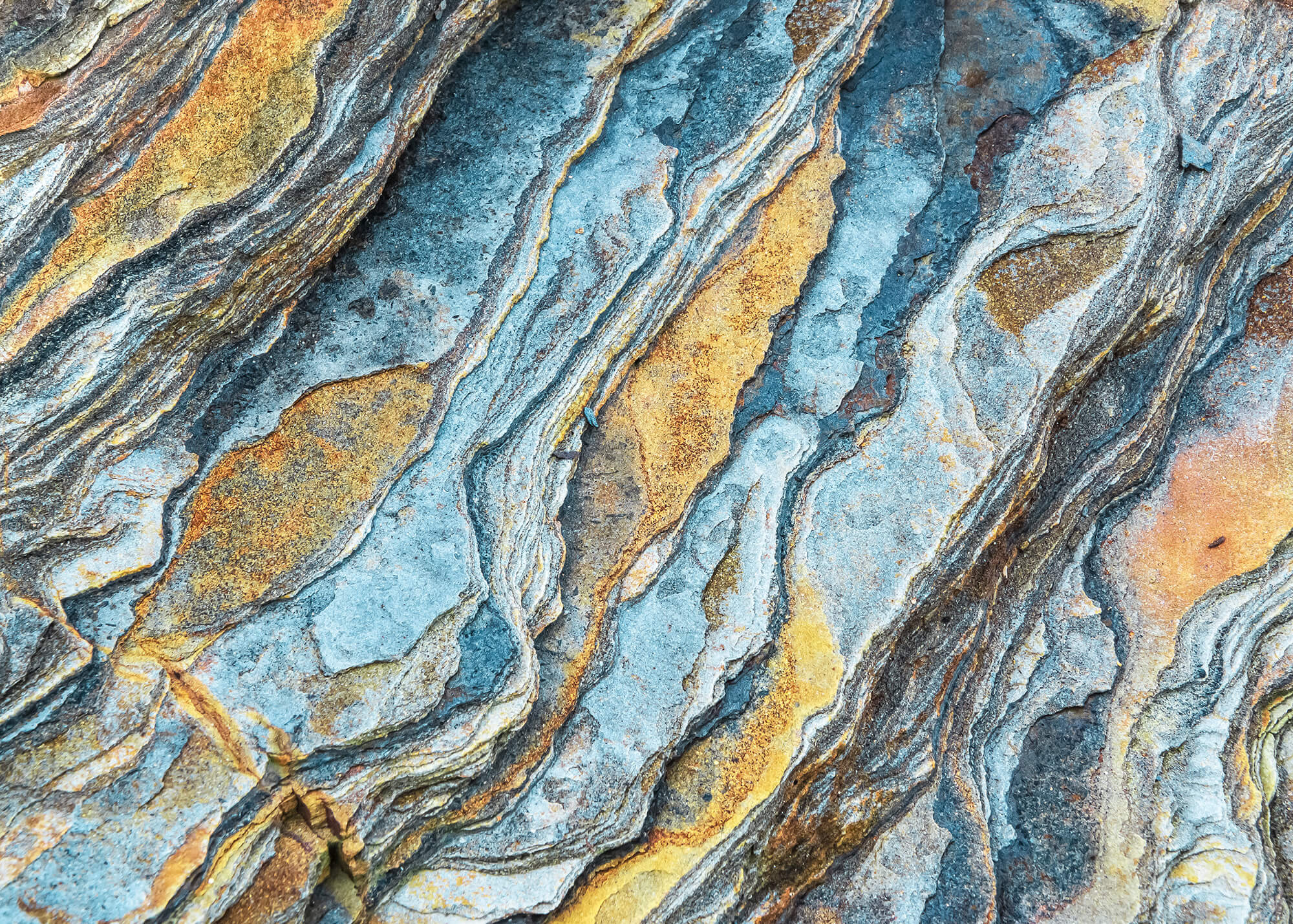
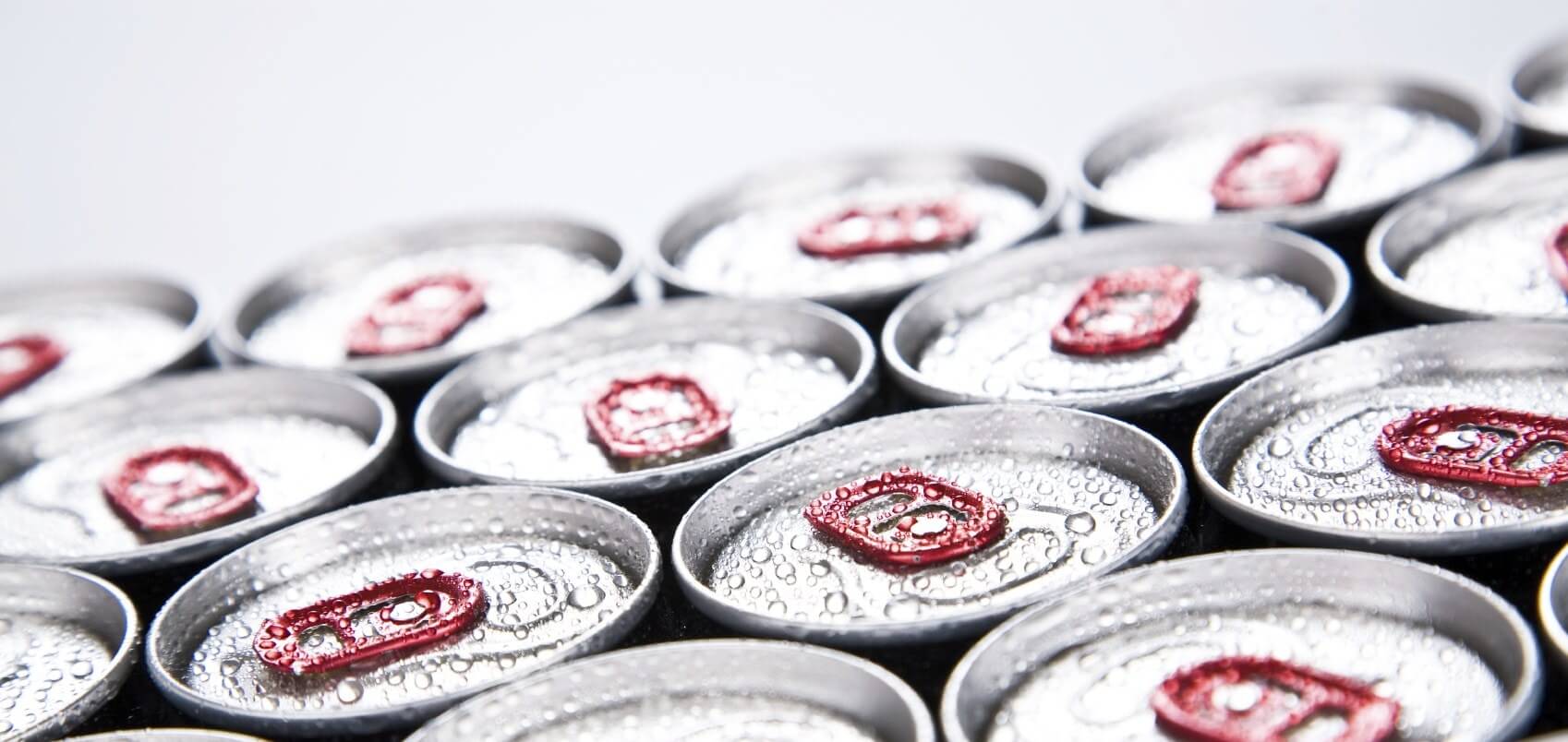
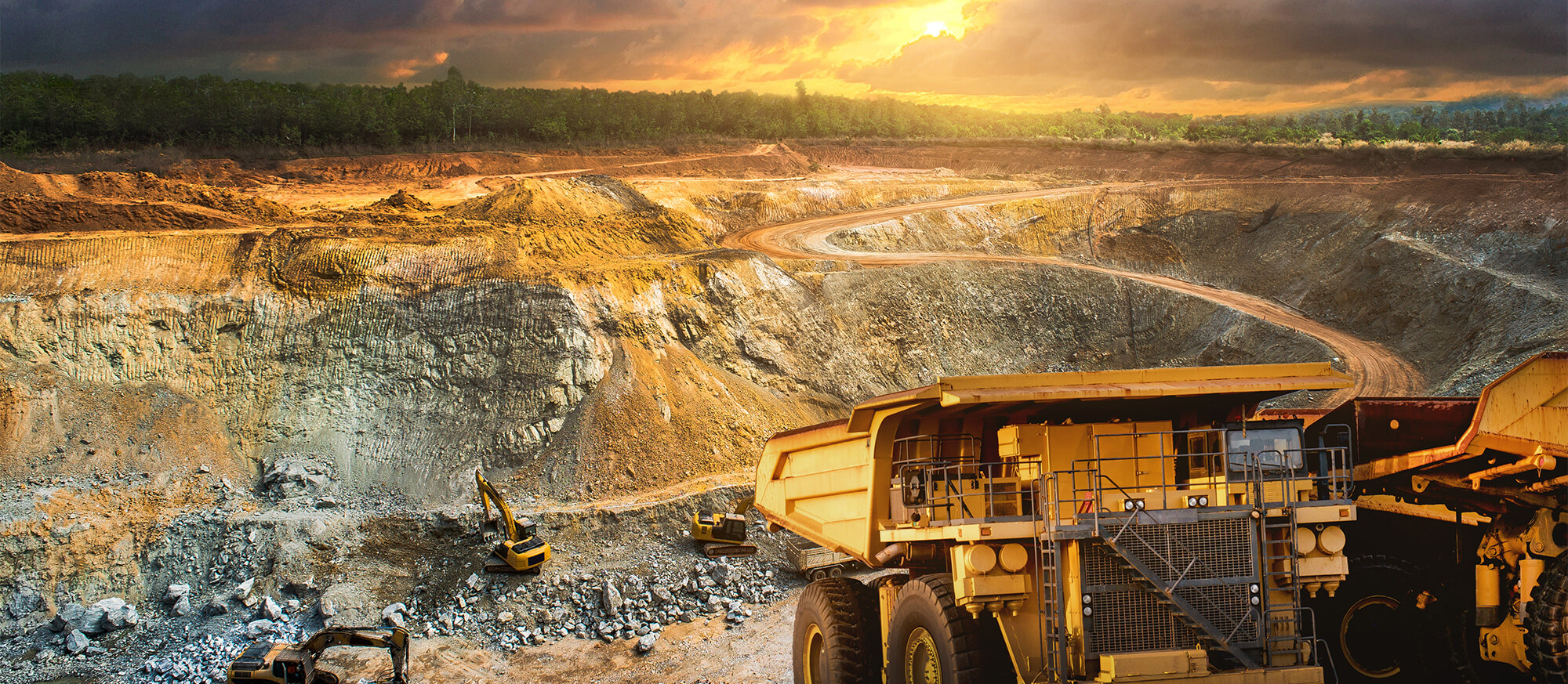
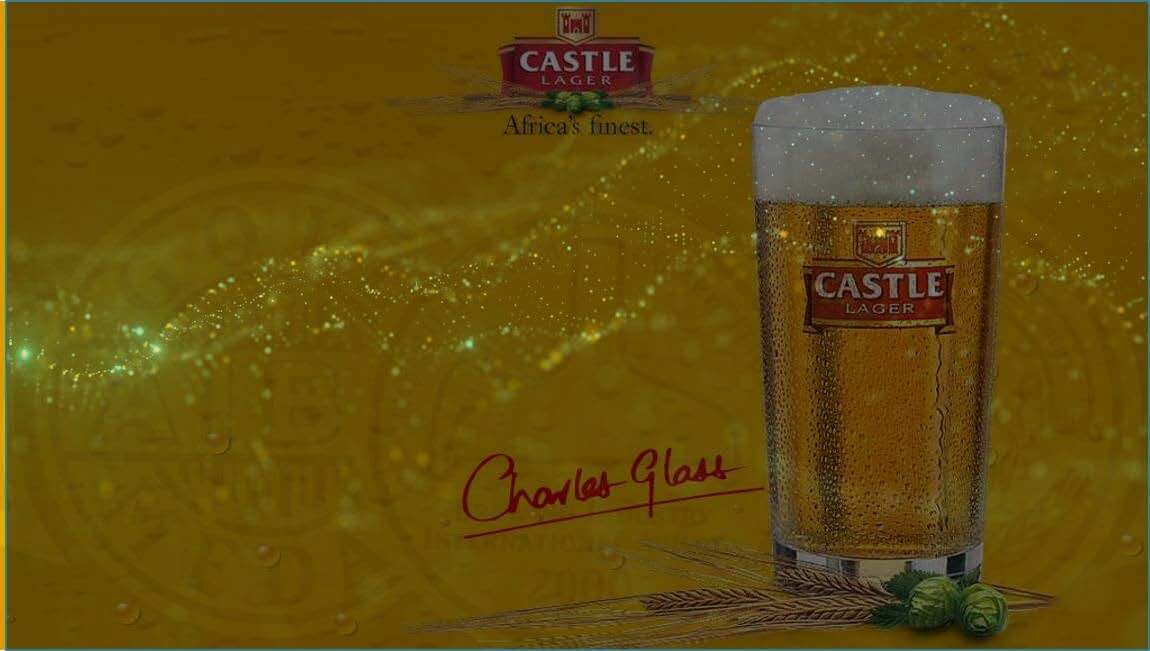
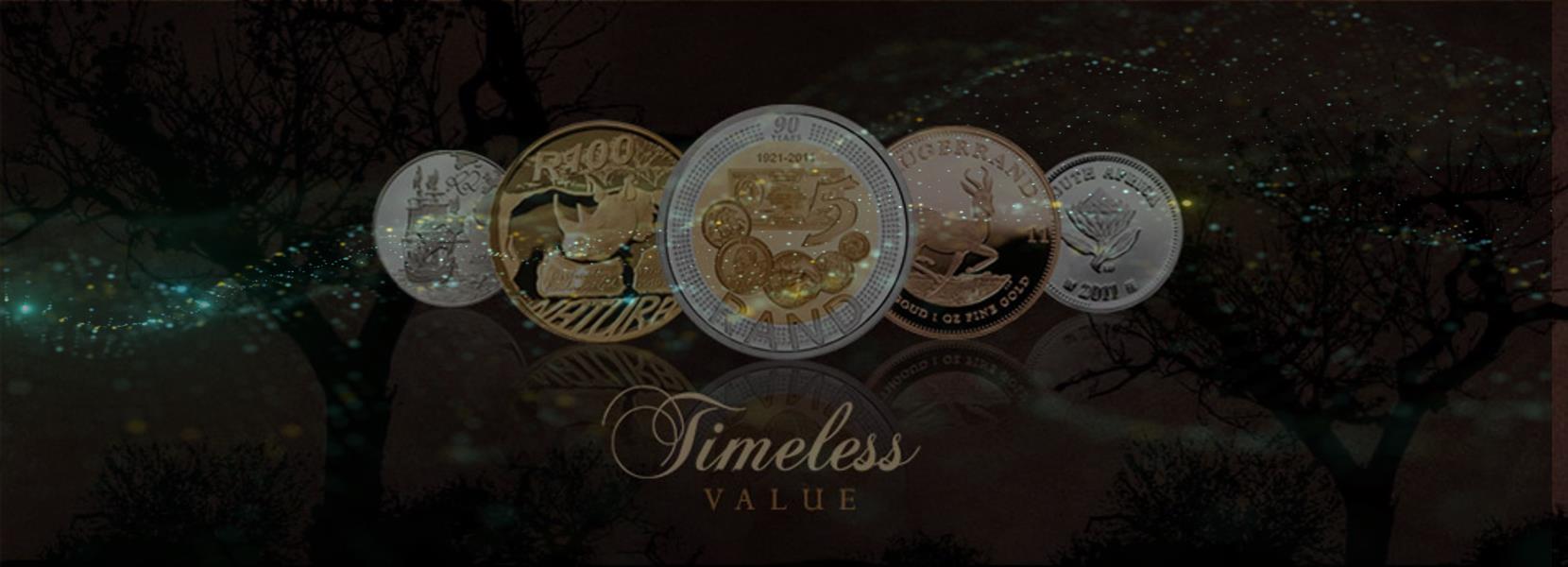
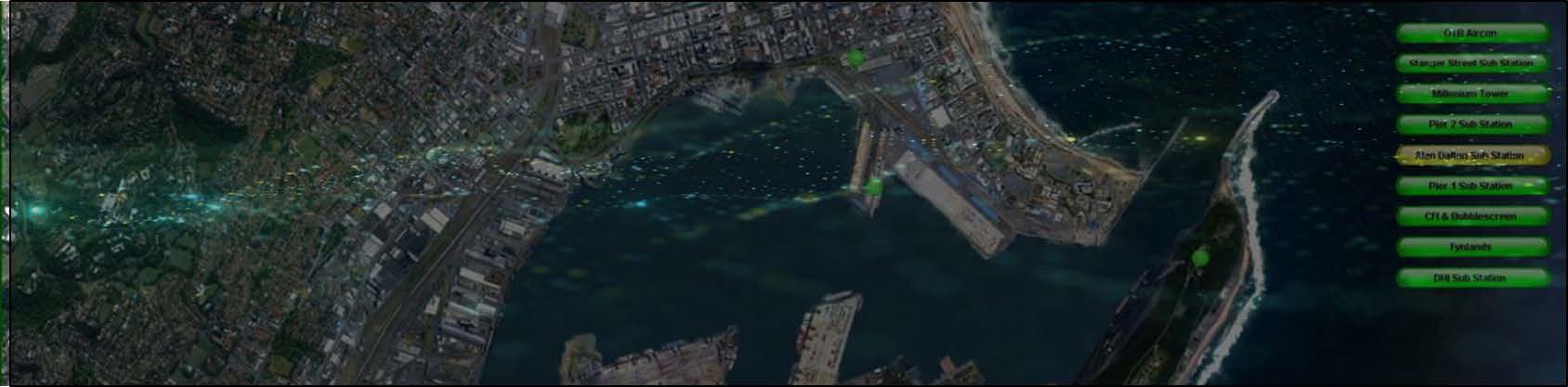
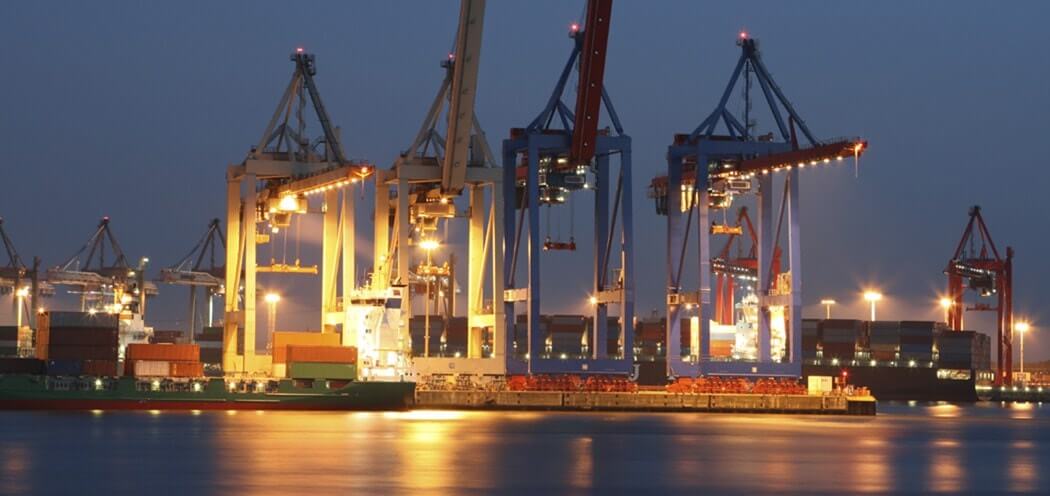
Speak to an Expert
Contact one of our highly qualified sales representatives to see how we can assist with maximising your potential!
AVEVA Historian from IS³ plays a central role in utilities management at Namibia Breweries
Goals
- Record critical production information from the solar, NH3 cooling, boilers, and CO2 plants as well as from the water and power meters
- Transfer production information to the existing DCS
- Develop a dashboard system for management to view consumption-related information linked to production volumes and KPIs
Challenges
- Getting the buy-in from all stakeholders
- Time synchronisation between the old Historian and the OPC server
Results
- CO2 sales targets met
- Compliance with municipal regulations
- Electricity savings
- Improved solar plant effectiveness
- Improved fault-finding
- Improved decision-making regarding plant requirements
- Better loss control
- Verification of the KPIs of new plant and equipment
- More accurate calculation and reconciliation of project KPIs and ROIs
Solutions and Products
- Historian
- Historian Client
- TOP Server
Windhoek, Namibia
Optimal utilities management contributes to a greener environment and a healthier bottom line at Namibia Breweries Limited (NBL) where AVEVA Historian from IS³ helps to generate daily, weekly and monthly consumption reports for water, electricity, chemicals, thermal energy, solar generation, carbon dioxide and air and to compare results with KPI targets.
Linking Historian tags to the company’s production system has also led to faster and more accurate problem detection.
Background
With regard to renewable energy, NBL has put into practice what others only talk about. The company has a 1MW roof-mounted solar plant with more than 4000 panels, 66 inverters and 4 cluster controllers. The whole system is connected to three of the company’s generator sections. When it was installed in 2013, it was the largest hybrid system in the world and it also made NBL completely self-sufficient regarding electrical power.
But this was only the start. Electricity, though a major component, is only one factor in the complex world of utilities which, today, are highly significant contributors to product costs, competitiveness and profitability. And there’s more to effective utilities management than simply watching the meter.
A Manufacturing Operations Management Survey conducted by LNS Research showed that the top two operational challenges for meeting Strategic Manufacturing Objectives were that companies had to deal with disparate systems and the lack of cooperation across their different departments.
“In our case, we have the brewing, packaging and distribution departments,” says André Engelbrecht, Manager: Industrial Control Systems, NBL “Each of them focuses on doing their job to the best of their ability but without necessarily much concern for the common denominator that makes it all possible; utilities.”
And so NBL decided to unify their various departments into a cohesive entity that could make real-time business decisions with regard to utility usage based on a single version of the facts.
The scope of the implementation would include access to the CO2 plant, NH3 Ammonia cooling, boiler house, water treatment plant, sterile air plant and power meters.
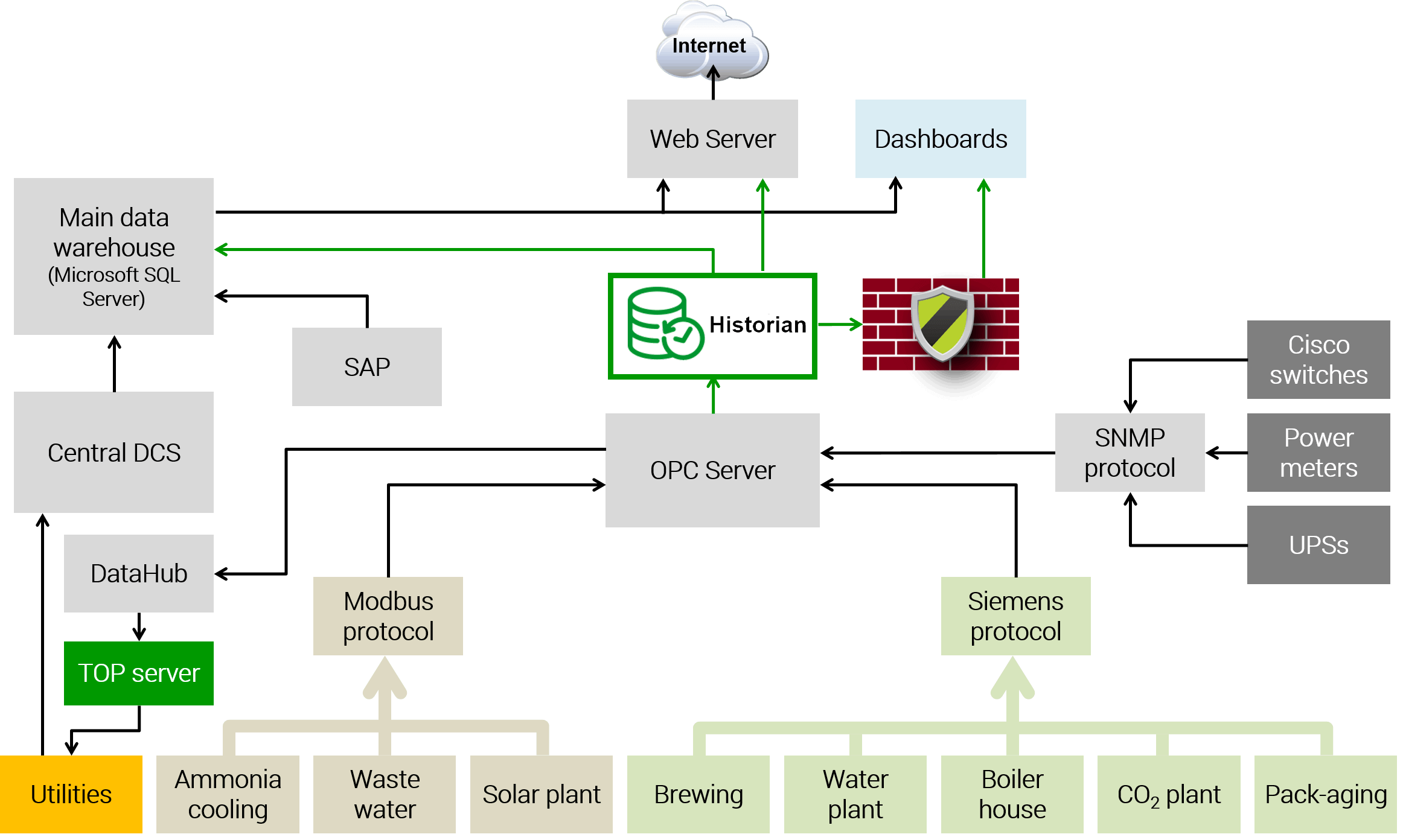
Implementation
The project was started in February 2015 and changeover to the new system was done after a two-week parallel operation during January and February 2016. But according to Engelbrecht, this is not the end as it is a “living” system designed to grow and supply the company’s information needs well into the future.
NBL has a central DCS which controls the beer-making process from beginning to end but achieving NBL’s goals of accurate decision support based on reality and real-time production information, more data collection and collation resources would be needed.
“It was vitally important that we got the buy-in from all stakeholders regarding the value of doing this, after which we decided to use the power of AVEVA Historian and the scripting capabilities of Historian Client,” says Engelbrecht.
“We also installed Software Toolbox’s TOP Server to retrieve data from our utility plants and systems and used the DCS to build a SCADA system. We then developed a web-reporting system for production personnel and a dashboard system for management. Most of our physical servers are now hosted in a virtual environment and this has made things a lot easier, such as time synchronization between the old Historian and the OPC server.”
NBL configured a virtual enterprise consisting of two TOP Servers (to balance the load of more than 100 PLCs and systems), one DataHub Server, AVEVA Historian, the main historian data warehouse and a web server. A secure HTTPS dashboard server enables management to view daily and monthly sales and operational KPIs from anywhere and weekly real-time stock volumes are sent to NBL’s advanced planning system using Historian Client queries. SAP files are imported daily regarding sales, production, logistics and depot information.
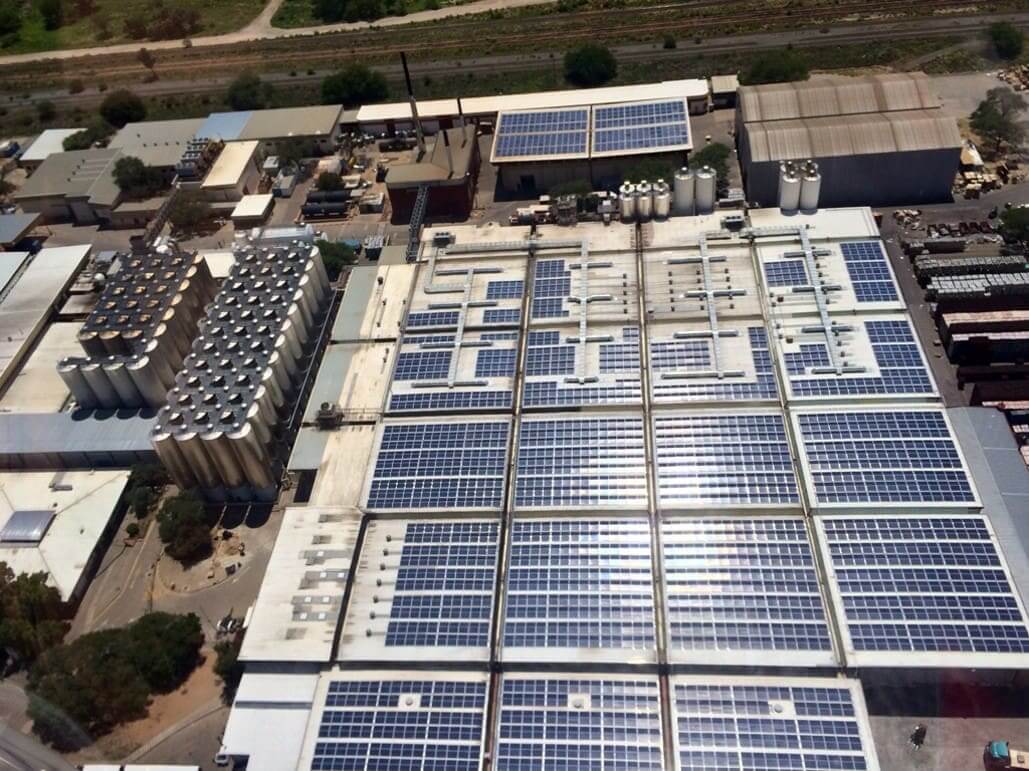
The system lets qualified personnel view various utility consumption and production information at the same time wherever they may be. They’re also able to view daily, weekly and monthly consumption information on the same platform. In future NBL will be able to switch off non-critical plant equipment to ensure that their maximum demand remains below target.
“It is great to see what can be done with technology and data when you use the right tools such as the [AVEVA] products we implemented in this project. It was also a great learning experience to combine the products we chose to enable us to make our end-results and user-experience better and more effective,” says Annemarie Kruger, MES/MIS Specialist, NBL.
“In my opinion, some of the most outstanding features of the system include its open standards, the wide range of drivers available, its scalability (as big as we want to go) as well as its ease of use, customisation and integration facilities with other initiatives,” adds Engelbrecht. “This implementation was all about 80% planning and 20% implementation. AVEVA’s Customer FIRST Support Programme is a must and the support from IS³ and Software Toolbox was outstanding.”
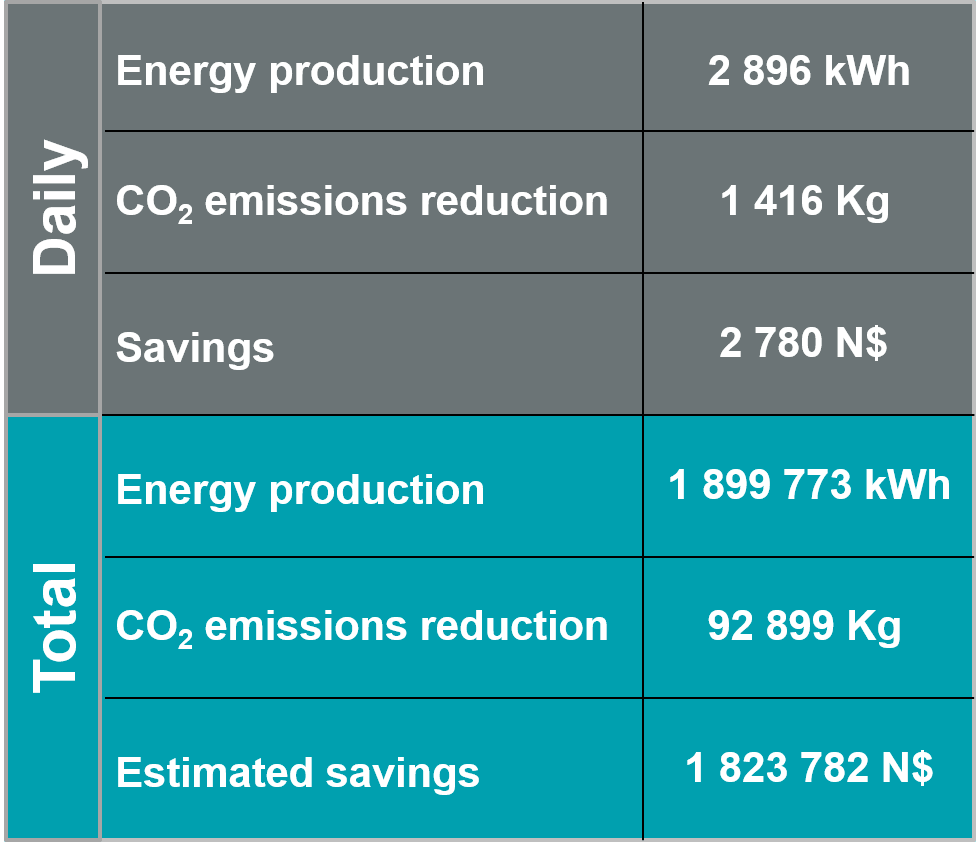
About Namibia Breweries Limited (NBL)
As part of the Ohlthaver & List (O&L) Group, the company is proud to uphold the tradition established in 1516 and brew their beer according to the Reinheitsgebot Purity Law resulting in products renown for their incomparable quality and purity.
The exceptional brands in their portfolio continues to garner international recognition, winning a series of gold medals during the prestigious Deutsche Landwirtschafts Gesellschaft (DLG) Awards.
And it’s quite a portfolio, comprising 11 brands including Windhoek, Tafel, Hansa, Heineken and Amstel to name a few.
In 2019, NBL celebrated its 100th birthday
AVEVA Historian from IS³ plays a central role in utilities management at Namibia Breweries
Goals
- Record critical production information from the solar, NH3 cooling, boilers, and CO2 plants as well as from the water and power meters
- Transfer production information to the existing DCS
- Develop a dashboard system for management to view consumption-related information linked to production volumes and KPIs
Challenges
- Getting the buy-in from all stakeholders
- Time synchronisation between the old Historian and the OPC server
Results
- CO2 sales targets met
- Compliance with municipal regulations
- Electricity savings
- Improved solar plant effectiveness
- Improved fault-finding
- Improved decision-making regarding plant requirements
- Better loss control
- Verification of the KPIs of new plant and equipment
- More accurate calculation and reconciliation of project KPIs and ROIs
Solutions and Products
- Historian
- Historian Client
- TOP Server
The System Platform’s Object Oriented Technology and centralised development environment means that plant objects are defined once, edited if necessary and immediately deployed to all their instances throughout the plant. No more running around with memory sticks.”
Paul Kotzé, EOHMM MES Specialist
Summary and conclusion
According to Coetzee, having the system integrator deal directly with the OEM turned out to be a “perfect” arrangement. “EOHMM talking directly with KHS went a long way towards eliminating misunderstandings, long lead times and other delays.”
Perhaps the single most outstanding feature of the implementation was the adoption of international standards (OMAC / PackML / ISA-95) and the adherence to internal standards (DPR). “Packaging line equipment manufacturers used to play it close to the chest with proprietary solutions that made us very wary because they would lock us in. But since they’ve adopted open standards, we are keener to buy these solutions because we know they will have interoperability and will be able to be integrated with other systems. So the irony is that the tactic of proprietary systems designed to lock in customers actually sold less then open systems with interoperability.”
Today’s MES implementations are a far cry from the “big bang” approach of the past. They can be installed gradually and the success of each incremental implementation measured before contemplating the next move while adherence to standards like ISA-95 ensure that all the pieces of the puzzle will actually fit together over time.
The accuracy of the downtime reports is such that even the OEM is using them to troubleshoot their equipment in preference to the manual tracking sheets they normally use when commissioning.”
John Coetzee, SAB Business Systems Manager, Manufacturing
AVEVA Historian from IS³ plays a central role in utilities management at Namibia Breweries
Goals
- Record critical production information from the solar, NH3 cooling, boilers, and CO2 plants as well as from the water and power meters
- Transfer production information to the existing DCS
- Develop a dashboard system for management to view consumption-related information linked to production volumes and KPIs
Challenges
- Getting the buy-in from all stakeholders
- Time synchronisation between the old Historian and the OPC server
Results
- CO2 sales targets met
- Compliance with municipal regulations
- Electricity savings
- Improved solar plant effectiveness
- Improved fault-finding
- Improved decision-making regarding plant requirements
- Better loss control
- Verification of the KPIs of new plant and equipment
- More accurate calculation and reconciliation of project KPIs and ROIs
Solutions and Products
- Historian
- Historian Client
- TOP Server
SAB manages the big picture with help from IS³
South Africa Breweries Limited (SAB), a division of AB InBev, is a vast, geographically-distributed network of breweries involved with complex production processes that have to satisfy the demands of millions of discerning customers in real-time. While this may sound challenging enough for the management of a single brewery, coordinating the efforts of seven manufacturing regions so as to provide an in-depth, unified and comprehensive vies of KPIs was best done with help from an application known as Enterprise Manufacturing Intelligence or EMI
Introduction
Before this project, there were limited facilities to proactively monitor critical systems in SAB’s beer manufacturing systems department and this led to the requirement for the implementation of a centralised monitoring system that would detect and warn about mission-critical manufacturing systems within SAB that were in difficulty with respect to meeting their KPIs.
Although distributed in nature, manufacturing enterprises such as SAB still need to operate as unified entities with respect to meeting their business objectives and it is in this regard that the company looked for a solution that would provide a collated picture of its production facilities and that made the best use of its existing information assets while providing the least change to operators and users.
Project objectives
Project Dash (short for the dashboard view it was to provide into the individual and collated production facilities of SAB) was started and it had to plug some important information holes by:
- Providing a centralised system for the early detection and warning of mission-critical problems
- Implementing a centralised data repository for analysis purposes
- Identifying key KPIs for PLCs, AVEVA Historian, System Platform and MES hardware and software systems for all seven beer manufacturing regions
- Presenting the information in dashboard format so that it could be easily read, interpreted and viewed from a divisional level at head office.
Solution selection
“We selected AVEVA Intelligence, supplied by IS³, because not only would it provide the functionality we were looking for but it would also fit into SAB’s strategic architecture and alignment with our standardising on the Application Server (part of AVEVA System Platform),” says Hein du Toit, Business Analyst at SAB Limited. “Buying into suite-based products gives long term value and it also gave us seamless access to time-based AVEVA Historian production data. It also allowed us to plug into MS SQL databases for MES and other applications.”
One of the main functions of any EMI application such as AVEVA Intelligence is to collate data from a wide and often disparate number of sources and to provide data warehousing, data aggregation as well as roll-up and drill-down functionality. But this information is less than helpful if it can’t be displayed in a format that is easy to define and understand. “[AVEVA] Intelligence provides user-friendly, drag-and-drop dashboarding functionality,” says du Toit. “Once you have explored the Dashboarding tool, Tableau Server, it really does make creating dashboards easy. It is an extremely powerful tool.”
Since it’s an SAB rule that all system integrator work done on the System Platform be performed by ArchestrA-Certified SIs, SAB chose system integrator Advansys for the implementation.
The accuracy of the downtime reports is such that even the OEM is using them to troubleshoot their equipment in preference to the manual tracking sheets they normally use when commissioning.”
John Coetzee, SAB Business Systems Manager, Manufacturing
Advansys has a good knowledge of the Food and Beverage industry in general and the brewing industry in particular. “[Their] specific advantage is knowledge of not only the beer making process but also the manufacturing system architecture that we use such as our eQMS, which is our quality/MES system,” says du Toit.
In addition, if any custom development had to be done, the expert use of the ArchestrA Application Object Toolkit was important. This gives the ability for any custom development to conform with SAB’s architecture and standards while making it easy for the engineers at regional level to understand and maintain the system.
“Lastly, AVEVA Intelligence is a Business Intelligence tool and Advansys’s knowledge of data warehousing was important to understand and implement the project on a tight timeline,” concludes du Toit.
Implementation
“Starting at the regional level, we wanted to make use of the existing infrastructure at the regions and did not want to introduce anything that would affect the performance of the historians, application object servers or even the PLCs,” says du Toit.
The project team drew up the required regional system architecture shown in figure 1 which collates KPIs from the PLCs as well as the Historians and MES servers for storage in the regional data warehouse from which it can be extracted and viewed in dashboard form according to the needs of users.
This regional architecture was replicated seven times for each of the regions and connected to the central data warehouse at head office, where the dashboard views not only represent an aggregated picture but also allow drilling down to the views of each region independently.
“SAB stipulated that we make use of the existing ArchestrA System Platform install-base, providing centralised change management, change propagation and it’s user-friendly Integrated Development Environment (IDE) for all data retrieval configuration,” says Advansys Director Graeme Welton.
The main reasons for this were that SAB didn’t want another system to maintain and ArchestrA is already the standard system control platform at all the breweries. Systems engineers are familiar with its IDE and the System Platform provides built-in change propagation and object derivation, a deployment installation model as well as an integral security model. In other words, everything was in place to allow Advansys to focus on the Intelligence application and not spend engineering time on fundamentals.
This phase of project Dash focused on collecting and collating diagnostic data with respect to system performance, traffic volumes, CPU usage, scan times, memory usage, message status (MSMQ), I/O Server item counts (total, active, etc.), disc space availability, unprocessed SQL messages and many more. This would include everything from the PLC, Server Platform, the process and the ArchestrA engine to the I/O Server, the file system, Microsoft Message Queue and any SQL database (MES).
“Because of the nature of this data, most of which comes from operating system diagnostics, as well as SAB’s requirement to use ArchestrA, we decided to use the ArchestrA Object Toolkit which gave us full use of the ArchestrA Object Framework and access to low-level C#.Net coding,” says Welton. “This approach also allowed us to use standard, out-of-the-box alarm and history primitives and compile editors for easy configuration. This all meant that no scripting was required for engineers to configure the data retrieval objects.”
Welton believes that the dashboard development tool is much more than it appears at first and that IS³ has produced a solution whereby almost anyone with some basic training can collect and collate information from virtually any combination of sources to suit their needs. “This is rather different from traditional Business Intelligence tools that require large IT teams to support and develop.”
Benefits
“I feel I should comment on three important aspects of the project,” says du Toit. “First of all, time; after the testing and development phase, we were able to roll out the project to the rest of the sites and commission within 2 months!
This is a reflection on the power of the underlying ArchestrA technology. Then there’s the matter of cost. The time saved with the project roll-out had a direct impact on the cost and we were able to finish within budget. The third point is the exceptional quality of the work delivered by Advansys.”
- One immediate benefit was risk reduction. With an immediate view of the status of each system, engineers were able to detect issues that impact performance of the various systems under scrutiny.
- Cross-platform comparison and analysis make decision making easy when deciding on deployment of areas.
- Cross-regional analysis shows trends and areas to focus on for development or where support should be given.
I believe that the dashboard development tool is much more than it appears at first and that IS³ has produced a solution whereby almost anyone with some basic training can collect and collate information from virtually any combination of sources. This is rather different from typical Business Intelligence tools that require large IT teams to support and develop.”
Graeme Welton, Director, Advansys