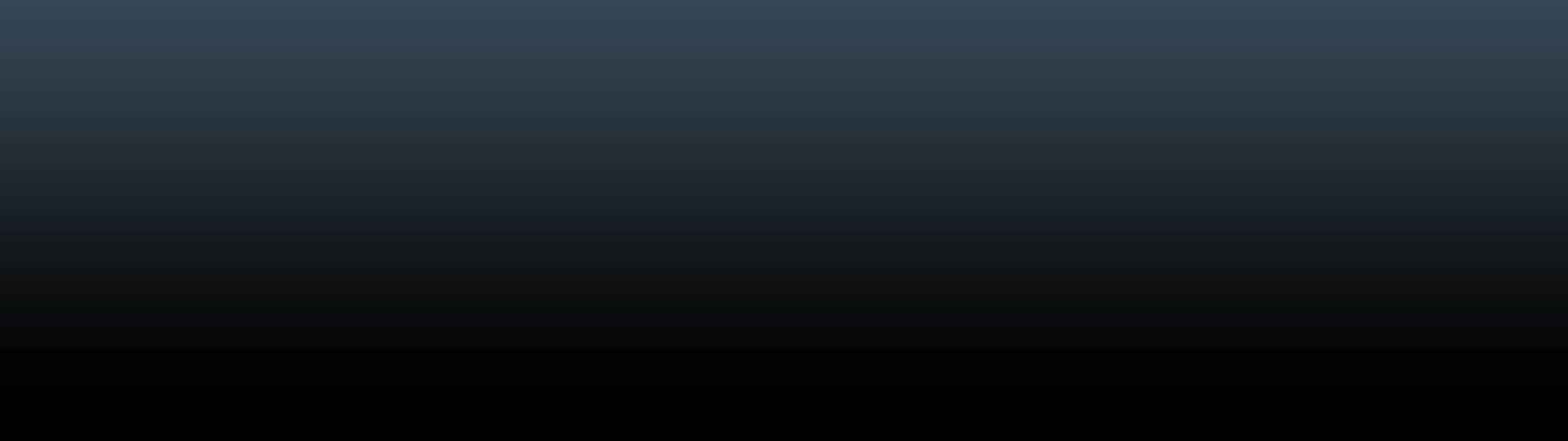
Schedule Confidently
Making sure that a refinery meets all its requirements – while remaining close to operating targets– is always a complicated task. Schedulers require decision-support tools that provide fast, accurate and transparent information on current and future activities. In addition, these tools need to have the flexibility to solve short-term problems, as well as highlight any drift from long-term goals.
As part of Spiral Suite, Schedule enables users to quickly set up and adapt their schedules for meeting their day-to-day requirements. Schedule also offers users the flexibility to meet their preferred way of working – via Gantt or table – or to add or modify activities quickly through integration.
Easy-to-use and fast-to-learn, Schedule’s familiar UI allows users to quickly adapt and evolve the schedule, even as requirements change.
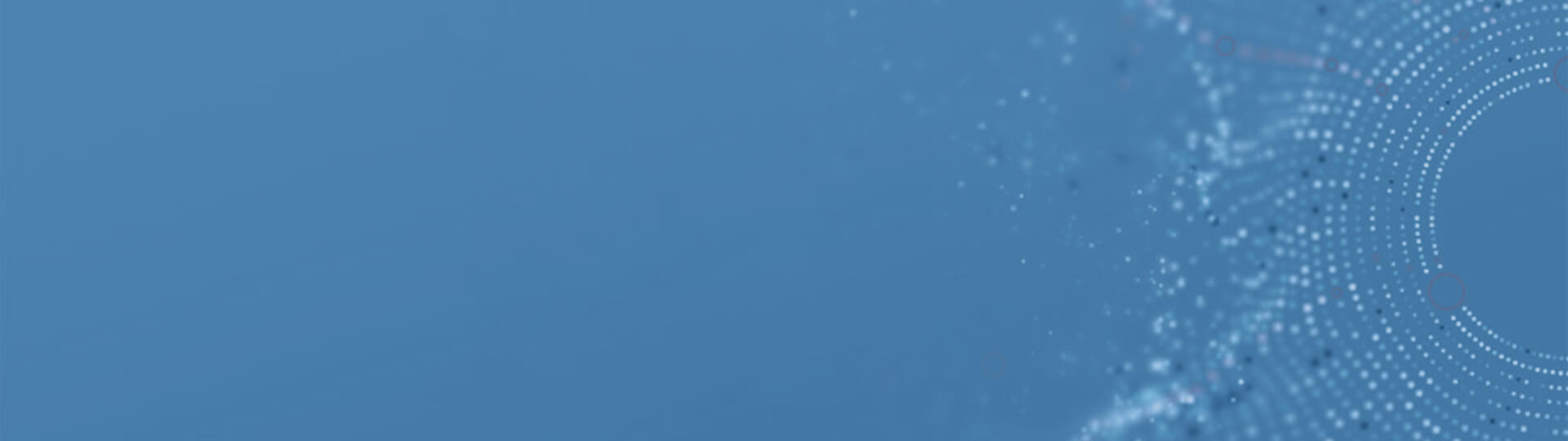
Supply Chain Scheduling
Sharing the same plant definition and mathematical engine as Plan allows for consistency. Users are empowered to comprehend the implications of their decisions on the business in its entirety, allowing them to concentrate on solving practical, short-term problems, highlight drift from long-term goals, as well as make the best possible use of the plant’s assets.